Monitoring Your IGC Compressor: Tips and Tools to Reduce Unnecessary Repairs and Replacements
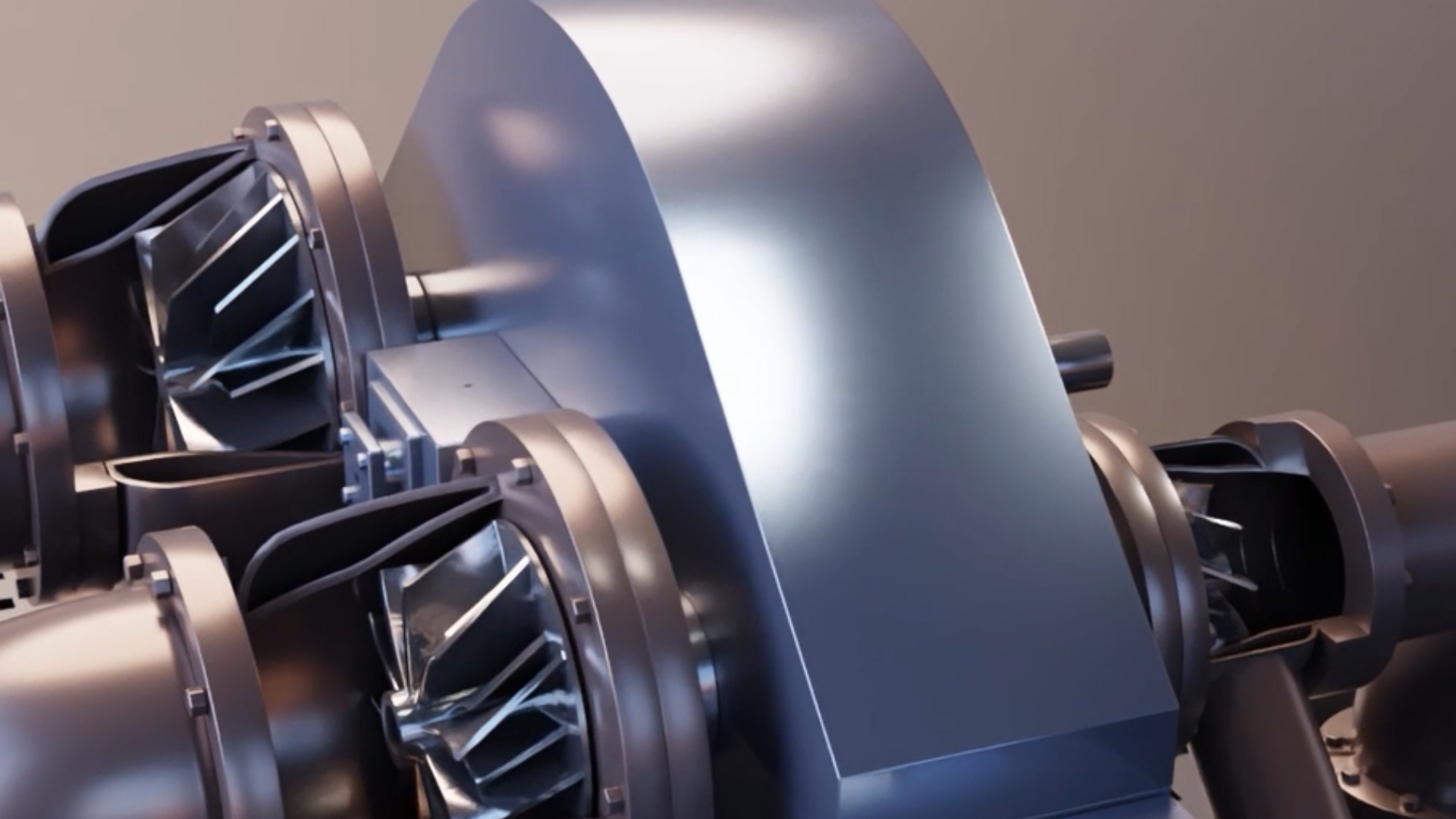
The IGC Compressor is used in various industries
Integrally Geared Centrifugal (IGC) Compressors are used in oil and gas, chemical processing, food & beverage, and other industries that require a constant pressure source at moderate pressures.
Understanding the IGC Compressor
The impellers of a multi-stage IGC Compressor are driven from the pinions associated with a gear box. A large bull gear drives the pinions at high speed. Pinion speeds typically range from 20,000 to 60,000 rpm, with some speeds going up to 100,000 rpm. The bull gears are typically driven by induction motors that operate between 1,500 and 3,600 rpm.
The impellers increase the pressure of the gas at each stage of the IGC Compressor. Considerable work is done at each stage, so besides the increase in pressure, the gas temperature also increases. In many designs, intercooling is provided between each stage to cool the gas temperature and to improve the performance of the IGC Compressor. The IGC Compressor provides a near constant outlet pressure, and thereby delivers uniform pressure to the plant. The stages of an IGC Compressor can also be called posts, so a three stage IGC Compressor is called a “three poster” and a four stage is called a “four poster”.
The Basics of IGC Compression Maintenance
Monitoring an IGC compressor should be more than scheduled maintenance.
● Visual assessments: Operators should ideally be doing a visual inspection at least once a month. This includes looking for major dents or cracks in the compressor, but also the electrical connections for signs of wear and tear.
● Temperature and pressure: An IGC Compressor is partially defined by its low-pressure system, though that doesn't mean it can always withstand production demands. The higher the temperature and pressure levels go, the shorter the lifespan of the compressor's components.
● Power consumption: Tracking the power consumption can give operators an idea of what patterns are normal, so they can take action if the machine requires an unusual amount of power for routine operations.
● Performance data: The performance of an IGC Compressor is determined by multiple metrics. If you're keeping track of everything from vibration to output pressure, you should be able to see what's causing a process slowdown or changes in quality.
● Vibration monitoring: Vibration monitoring for IGC compressors is a way for operators to track how the machine behaves during normal operation and when process changes take place. By understanding the vibratory behavior of the IGC Compressor, one can take action when they see changes in vibration before those issues become detrimental to the machine.
Tools and Techniques for Effective Monitoring
In addition to visual inspections and operator analysis, the right monitoring equipment can make a huge difference to the lifespan of your IGC compressor. Pressure and temperature sensors can be placed on key sections of the machine for an accurate reading of how they are changing over time. Likewise, vibration sensors properly placed will provide enormous value for the condition of the machine. At a minimum, IGC Compressors should come with at least one proximity sensor near each impeller to report vibration levels. This vibration sensor suite can be enhanced by orthogonally placing proximity probes near each impeller, adding thrust position and axial vibration monitoring, as well as speed monitoring of the bull gear and each of the pinions.
You can also rely on power monitoring devices and data analysis software to reflect how the IGC Compressor is handling inevitable shifts in daily operations. For instance, if operators have a week where production volume is doubled, the right technology can not only collect and log the numbers, but it can also provide notifications of abnormal events. It gives operators the insight they need to intervene quickly.
Benefits of Proactive Monitoring
The most obvious benefit of proactive monitoring, including vibration analysis and performance evaluation, for a centrifugal air compressor is its ability to detect potential issues. Pressure and flow monitoring improve operational efficiency and stave off expensive repairs.
At Metrix, the goal is to put pertinent information into the hands of our customers, so they can make accurate decisions about the machine’s health.
Vibration, temperature, and pressure monitoring are full-time jobs that can be complicated by anything from false alarms to power outages to fluke interactions between gears. If you're looking for equipment that was engineered to account for nearly every event, Metrix offers a complete line of vibration sensors and transmitters to help meet your needs. Please contact us if you have any questions regarding your condition monitoring needs.