Vibration Monitoring of Pumps
Pumps are some of the most popular mechanical devices and an integral part of the plant. They are widely used in various industries to transfer liquids, increase pressure, or circulate fluids within systems. They play a crucial role in numerous processes, including oil and gas production, chemical processing, water supply, water and wastewater treatment, cooling systems, and more.
Pumps move liquids from one area to another by accelerating the liquid using centrifugal forces in Centrifugal Pumps, or by grabbing a certain amount of liquid and physically pushing it towards where it needs to go using Positive Displacement Pumps. Positive Displacement pumps are further categorized into Reciprocating and Rotary Pumps.
Maintaining pumps helps them last longer, and it also makes it possible to avoid process slowdowns that ultimately affect production. When you prioritize vibration monitoring for pumps, you can expect to see a notable difference in your operations by observing the condition of your rotating and reciprocating assets. Monitoring for significant changes in vibration allows you to take action before you have serious machine degradation.
Pump maintenance comes down to identifying and interpreting the forces that impact the pumps. Equipment reliability depends on how the different parts of the pump work together to operate successfully. If the pump experiences issues such as worn bearings, shaft misalignment, pump cavitation or other defects, it will have an impact on the vibration levels, and on the normal operation of the pump. Vibration monitoring sets a baseline for operators and technicians and helps them understand when a problem begins so that it can be addressed as early as possible. Instead of reacting to a mishap, they can proactively control the situation before it has the chance to develop further.
Please see below for a variety of vibration monitoring solutions for pumps from Metrix so that you can find the right one for your needs.
Monitoring Small Horizontal & Vertical Pumps with Rolling Element Bearings
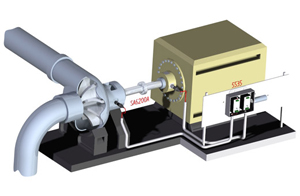
SA6200A Accelerometer and 5580 Signal Conditioner
The SA6200A Accelerometer provides an acceleration signal output proportional to 100 mV/g to the 5580 Signal Conditioner. The 5580 Signal Conditioner can do a number of things with the signal that are very useful for pumps and motors. In Channel 1 of the 5580, the acceleration signal can be used to monitor bearing condition, while Channel 2 can be used to monitor integrated velocity for rotor related faults like unbalance, misalignment, cavitation, etc. The 5580 provides two 4-20mA outputs for interfacing with Programmable Logic Controllers (PLC), Supervisory Control and Data Acquisition (SCADA) System and other control systems. The dynamic signal is available from the front panel for vibration analysis purposes, as well as from the terminal block to provide the dynamic signal to a monitoring system up to 300 meters (1,000 ft) away. The 5580 can be configured in the field for scale ranges, filters and display indication. These products can be used in hazardous areas.
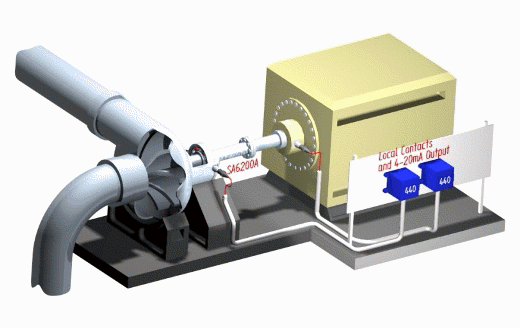
440 / 450 Vibration Switch with External Sensor
The 440 Vibration Switch can be configured for both an internal and external accelerometer sensor. The 440 features the ability to set limits on the vibration amplitude for both alert and danger. It provides local contacts as well as a 4-20mA output for interfacing with Programmable Logic Controllers (PLC), Supervisory Control and Data Acquisition (SCADA) System and other control systems. The external sensor is usually located on the pump bearing nearest the coupling, the 440 switch is located in a more electronic friendly environment. These products can be used in hazardous areas.
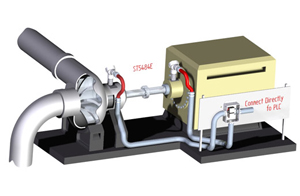
ST5484E Velocity Transmitter and ST5491E Indicating Transmitter
The ST5484E provides for the simplest installation available on the widest number of machines in industry. Its proportional velocity output is perfect for machines that operate at 60 Hz or less. It's one of the few transmitters that are accurate down to 2 Hz. Since it’s a loop-powered device, only two wires are needed for full operation. The ST5484E outputs a 4-20mA signal to Programmable Logic Controllers (PLC), Supervisory Control and Data Acquisition (SCADA) System and other control systems. Optional filtering and dynamic outputs are available. The ST5491E has a local indicator and has all the features of the ST5484E. These products can be used in hazardous areas.
Monitoring Large Vertical Pumps with Rolling Element Bearings
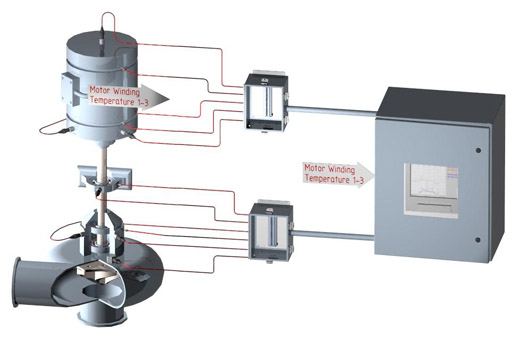
Large vertical pump applications, such as the one shown, require a more thorough monitoring scheme than smaller applications.
Metrix provides vibration sensors for all bearings and a Datawatch Monitor. The Datawatch monitors all vibration and temperature readings and compares them to pre-programmed setpoints in order to change the state of alarm and danger relay outputs.
The sensors can include SA6200A accelerometers or SV6300 velocity sensors, both going to a 5580 or SW5580 Signal Conditioners, with the 4-20 mA outputs going to the DataWatch Monitor, or Programmable Logic Controllers (PLC), Supervisory Control and Data Acquisition (SCADA) System and other control systems. One could also use the ST5484E or ST5491E directly to the DataWatch Monitor.
Monitoring Large Horizontal & Vertical Pumps with Fluid Film / Journal Bearings
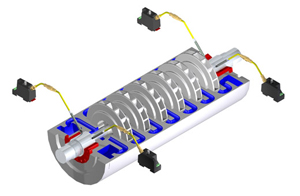
Journal bearings use a layer of oil to isolate the shaft from the bearing. Therefore, the shaft is actually floating on a cushion of oil and has no contact with any other metal. Because of the oil layer, a vibration signal produced by the shaft does not have a path to travel to the machine casing. That means that a seismic sensor placed on the case of the pump cannot properly sense what is going on with the shaft.
This makes it necessary to use proximity sensors to detect shaft faults. A proximity probe mounts through the case of the machine and senses the position of the shaft relative to the probe tip. A 5497PM probe holder is usually used to support the probe through the casing. The pump casing holds the probe holder steady so that any movement in the shaft will cause the proximity probe to output the proper measurement. The Metrix Digital Proximity System (DPS) can provide either a dynamic signal output to a monitoring system using the MX2033 Driver or to a Programmable Logic Controllers (PLC), Supervisory Control and Data Acquisition (SCADA) System and other control systems using the MX2034 proximity transmitter. This type of measurement is termed “relative” because the shaft movement is being measured relative to the machine casing.
These products can be used in hazardous areas.