Premier Industrial Shakers
The Hardy Shaker ensures that our Seismic Sensors and Transmitters work properly and give you the results you need. Just like the pressure and flow instruments in your facility require calibration checks every year, so do your Seismic Sensors and Transmitters.
This system puts the calibration check of Seismic Sensors and Transmitters in your control. As a cost-effective maintenance strategy, this predictive and proactive approach is better than a run-to-failure strategy. The entire premise of a predictive and proactive maintenance program is based on the reliability and integrity of the transducers providing the information.
If the Seismic transducers are not working properly, you will not receive the value you are expecting to produce the return on investment that you have already made. The Hardy Shaker is necessary to ensure your proactive maintenance strategy is effective. The Hardy Shaker comes in two models - HI-903 and HI-913 for your convenience.
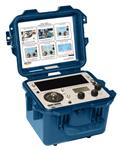
HI-903 Hardy Shaker
Deluxe model with storage and automated reports.
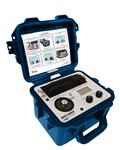
HI-913 Hardy Shaker
Standard model for heavy duty field use; with ruggedized case.
Why Are Industrial Shaker Tables So Important?
Seismic sensors and transmitters are designed to give you an easy way to check some of your most important equipment. Engineers and technicians rely on warning systems to understand when their machinery is beginning to falter, whether due to the general wear of time or an unexpected spike in vibrations. If these sensors and transmitters fail to report the correct information, it can wreak havoc on an organization.
An industrial shaker machine is the key to calibrating these instruments, so they can effectively relay the proper measurements. By mimicking real-world conditions, staff can get a sense of how equipment would respond when they’re under intense pressure. The oil & gas industry, power generation, water and wastewater, automotive, electronics, and food industries all rely on portable shakers to analyze their equipment’s performance and determine the reliability of their machines.
Types of Vibration Shakers
There are multiple types of vibration shaker tables on the market:
● Mechanical: Mechanical sensors can rely on weights, centrifugal force, or motion control to create vibrations.
● Electrodynamic: Electrodynamic shakers use coils and magnets to pass currents and create vibrations.
● Hydraulic: Hydraulic vibration shakers use oil pressure to trigger the necessary reactions.
The right type of portable shaker will depend on the application. An electrodynamic shaker will be faster and quieter, but it won’t have the same force capacity as a hydraulic shaker. A mechanical shaker may be cost-effective, but it may not produce the more accurate results of a more advanced model.
Product Ranges and Specs
The Hardy Shakers from Metrix include the following specs.
HI-903
● Wide frequency range: 7 Hz to 10 kHz (420 to 600000 CPM)
● Internal memory to store calibration data and USB flash drive output
● Certificate of calibration with supplied Excel template
● Complete turnkey system
● Easy transport via Pelican® Storm Case
HI-913
● Transducer verification from 7 Hz to 10 kHz
● Compact and self-contained (made for accelerometers, velocity transducers, and proximity probes)
● Easy transport via Pelican® Storm Case
● Carbon fiber composite armature flexure to withstand forces
Metrix shakers are accurate even in the midst of intense testing. If you need sensors and shakers that can tell you how your machinery will perform under different scenarios, our products have been shown to help our clients get the results they need.