Condition Monitoring Sensors
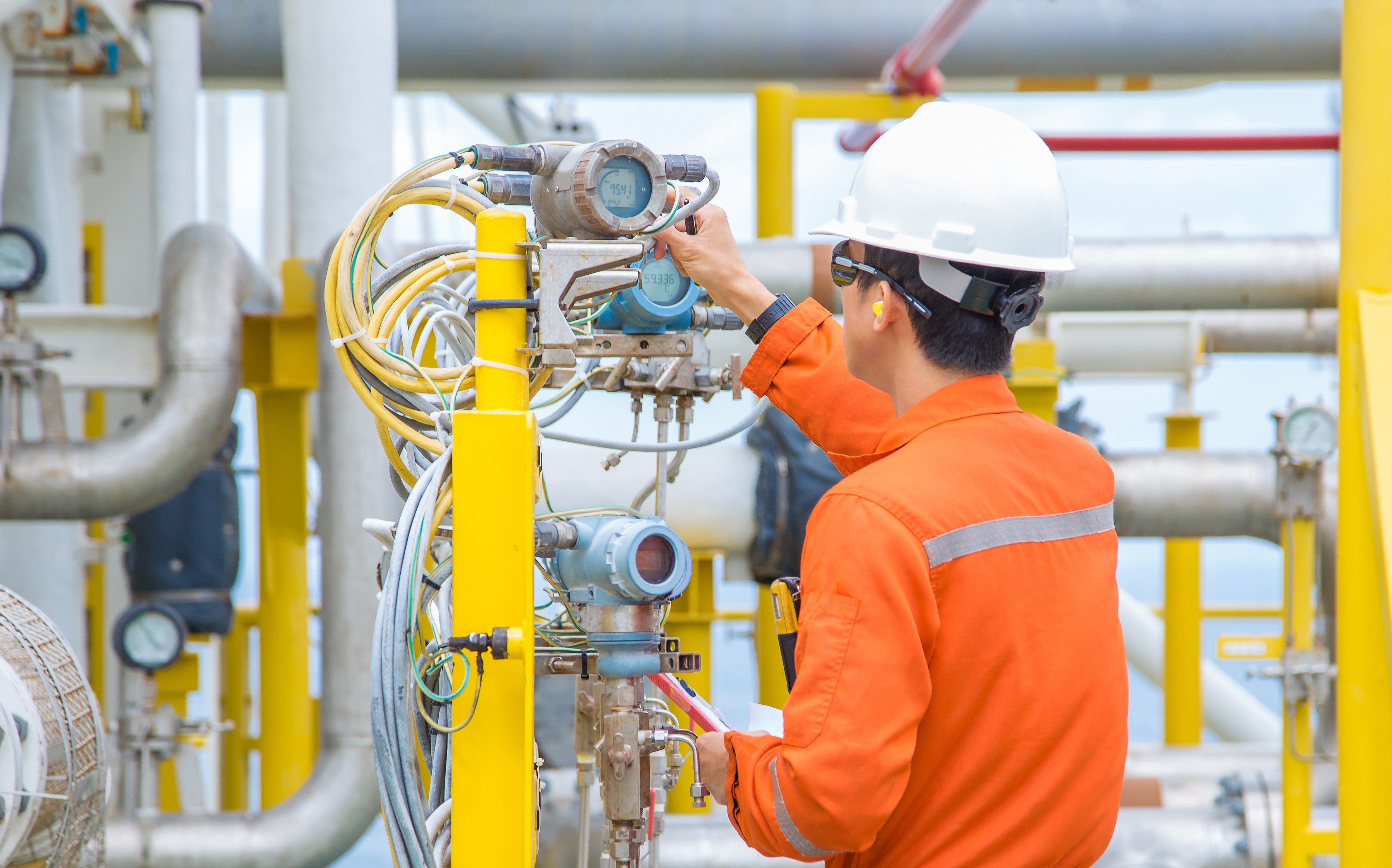
Condition monitoring sensors are essential for reducing costs and increasing safety
Condition Monitoring Sensors
Metrix is an experienced leader in the condition monitoring and asset protection industry.
A condition monitoring system is an important component in improving quality assurance and safety, especially for industrial operations involving rotating and reciprocating machinery. These systems allow a technician or an automated process to keep a watchful eye on the operating conditions of valuable equipment, ensuring they’re running correctly and within an established tolerance without unexpected production downtime. Metrix provides early warning of a machine problem, so you can take action and perform machinery diagnostics when you need to.
Condition monitoring can look quite different from site to site. It can be a simple matter of placing a single vibration sensor that trips an alarm when a machine goes out of tolerance, or, it can be achieved with a complex network of many sensors that may interface with cutting-edge software platforms. Metrix specializes in providing products for the oil and gas, petrochemical, pipeline, air separation, power generation, cooling tower, water/wastewater, and chemical industries. Our focus on these market segments allows us to deliver quantifiable business results to our customers on a global scale.
No matter how sophisticated or basic a condition monitoring system is, it all begins with installing electronic sensors near the monitored equipment.
What Are the Types of Condition Monitoring Sensors?
There are multiple types of condition monitoring sensors, each of which works a bit differently to accomplish its primary goal of ensuring the process and the machines continue to work properly.
● Vibration Sensors. Historically, seismic sensors were created initially to help society predict seismic wave activity that could lead to catastrophic earthquakes. Now, we have repurposed those seismic sensors to measure the casing vibration on rotating and reciprocating machines. Vibration in industrial equipment can be a sign of many potentially serious problems. Vibration sensors often provide overall vibration levels, indicating whether your asset is under stress, but they can also give more sophisticated readings, these sensors are ideal both for monitoring applications – getting instant notification when faults occur and more in-depth analysis that vibration experts can do with trended vibration data.
Metrix advocates a vibration monitoring solution that makes economic sense for the machine’s impact on the plant. For critical production limiting machines we advocate a sensor solution that monitors each bearing or throw, thrust, and speed on rotating or reciprocating machinery. For non-critical rotating or reciprocating machinery that marginally affects plant production, we advocate a minimal sensor solution for monitoring and protection, or depending upon the asset, an electronic or mechanical switch for protection.
Our solution depends upon the customer’s cost of Unscheduled Downtime. Unscheduled Downtime caused by a problem coming from a rotating or reciprocating machine is the costliest for a plant. The plant loses money from lost profits (Lost Opportunity Cost = loss of profitable output), expedited repair, material and labor costs, standby labor costs, quality issues, customer trust / delivery issues, and most importantly personnel safety concerns.
● Temperature Sensors. Condition monitoring systems can help to keep sensitive equipment operating within a specific temperature range. A temperature sensor is an electronic device that measures the temperature of its environment and converts the input data into electronic data to record, monitor, or signal temperature changes. They may also be designed to automatically shut down equipment when it overheats, potentially saving it from costly replacement.
● Tilt Sensors. For devices that rely on spinning parts, it can be crucial that they are mounted on a level surface. Inclinometers, also called tilt sensors, measure the slope or angle or tilt of objects based on gravity in various applications. When such devices begin to go out of level, the constant inertia of the spinning can quickly exacerbate the problem. Tilt sensors let you know about even minor changes in level so that the plant can take action and prevent any long-term problems.
● Pressure Sensors. Industrial components often operate under very extreme conditions. A pressure sensor is an electronic device that detects, regulates, or monitors pressure, and converts pressure data into an electronic signal. When pressures are abnormal, you not only see changes in the pressure sensors, but the vibratory condition of the machine changes, which can be sensed by the vibration sensors.
● Water or Liquid Sensors. Applications that require a steady supply of water or other liquid to keep other equipment or systems supplied, cooled, lubricated, or otherwise hydrated or full will require flow sensors. A flow sensor is an electronic device that measures or regulates the flow rate of liquids and gasses within pipes and tubes. Flow sensors generally use differential pressure or stress, or changes in electromagnetic signature and some even include laser technology. These measurements can also be interpreted by computers and digital interfaces to measure flow. This helps to ensure the correct amount of liquid is getting from point A to point B. A condition monitoring system using liquid flow sensors ensures that pumps can be shut off before they lose flow and necessary pressure head, as well as preventing pumps from running dry, which could eventually destroy the pump entirely if allowed to continue. Vibration monitoring is also very useful to detect these trouble conditions.
● Photosensors. Even a simple light-detecting sensor like the one that automatically flicks on your outdoor lights at sunset can be used in condition monitoring systems. For example, a dark area where motors run without human intervention might be monitored for fires using a photocell.
Multi-Sensor Condition Monitoring Systems
Today’s cutting-edge conditioning monitoring systems often rely on a complex network of several different types of condition monitoring sensors.
Metrix has been the preferred supplier of industrial vibration monitoring systems to many of the world’s leading manufacturers and end-users, a trusted and reliable source of condition monitoring sensors and other components to keep your rotating and reciprocating machinery running safely and properly. Contact us today to see how a robust condition monitoring solution can improve your quality and safety processes.