How Vibration Monitoring Can Extend the Life of Your Pumps
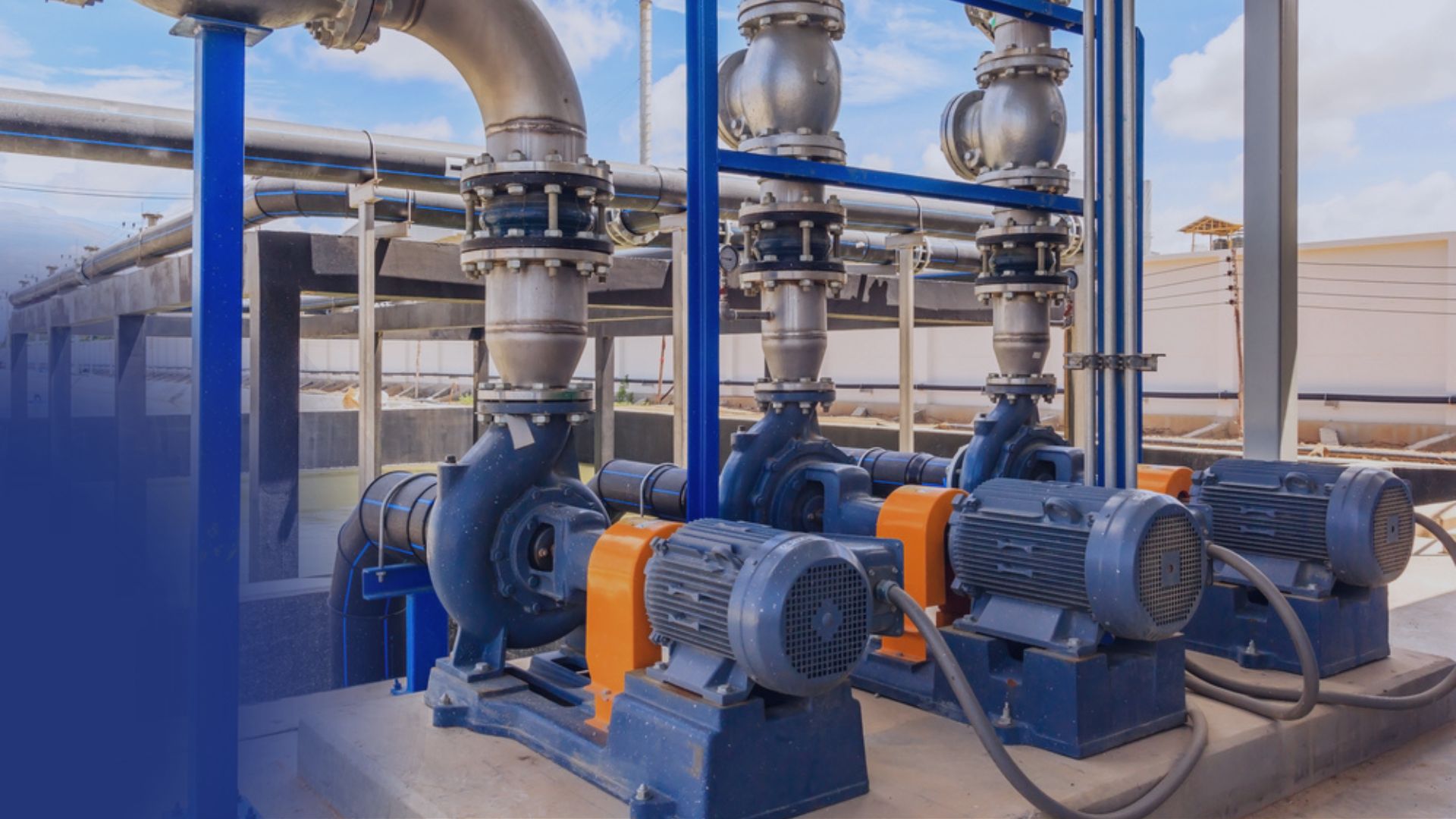
Extending the life of your pumps can ensure optimal performance, resulting in reduced costs
Pumps are an essential equipment in many industrial processes, and they are subject to significant wear and tear over time. One way to extend the life of pumps and ensure their optimal performance is through vibration monitoring. Vibration monitoring allows you to detect potential problems early, enabling you to take corrective action before they become more serious and costly.
What is Vibration Monitoring?
Vibration monitoring is the process of measuring the vibration levels of machinery and equipment to determine if they are operating within safe and acceptable limits. Vibrations can be caused by a variety of factors, such as unbalanced loads, misalignment, bearing wear, and damaged components. By monitoring vibration levels, you can identify these issues and take corrective action to prevent them from causing further damage.
How Vibration Monitoring Benefits Your Pumps
Early Detection of Problems: By continuously monitoring vibration levels, you can detect potential problems early before they cause significant damage to your pump. For example, if the vibration levels of your pump suddenly increase, it can be an indication of an unbalanced load or possible bearing wear. If left unchecked, these problems can lead to premature wear and tear of the pump’s components, leading to costly repairs and downtime. With vibration monitoring, you can detect these issues early and take corrective action before they become more serious.
Predictive Maintenance: Vibration Monitoring can also help you implement predictive maintenance programs. By monitoring vibration levels over time, you can establish baseline measurements and track changes in vibration levels. These changes can be used to predict when maintenance is required, enabling you to schedule maintenance during planned downtime rather than waiting for an unexpected breakdown.
Improved Efficiency: When a pump is operating outside of its optimal range, it can cause excessive vibrations that lead to premature wear and tear. By monitoring vibration levels, you can identify when a pump is operating outside of its optimal range and take corrective action. This can include increasing the pump’s suction pressure, adjusting the pump’s speed or flow rate, reducing the load on the pump, and or replacing worn components. By optimizing the pump’s performance, you can extend its life and reduce energy consumption.
Reduced Downtime and Costs: When a pump breaks down unexpectedly, it can cause significant disruption to your operations, resulting in lost production and revenue. By monitoring vibration levels and taking corrective action early, you can prevent unexpected breakdowns and reduce the amount of time and money spent on repairs and replacements.
Common Issues that Cause a Change in Vibration
A change in vibration trends can indicate there is an issue with your pump. The issues can include changes in forces or supporting structures within the pump. With the help of a trained technician, the issue can be diagnosed before it causes irreversible damage or pump failure. Common issues that can be detected with a vibration sensor include:
Pump Bearing Issues: One of the most common causes of pump vibration are worn bearings, which could be a result of excessive load or improper lubrication. Though a pump may be designed to be operational for 20,000 hours, the bearings are not likely to last that long if they’re not properly loaded and lubricated.
Bent Shaft: A vibration sensor can detect a bent shaft in your pump because it may cause high radial and axial vibration. The axial vibration that may also correlate with axial phase differences from end to end. The bent shaft will also cause 1X (1X vibration is the vibration at the machine’s running speed) radial vibrations due to the unbalance.
Pump Cavitation: Cavitation is usually a result of low suction pressure. With cavitation, it will feel and sound like gravel is being tossed around inside the pump’s interior. Distinctive popping may also be heard as the pump operates. This fault causes damage to the rotor and housing.
Pump Flow Pulsation: This error may occur when the pump is working close to its shutoff head. This will cause variations in pressure head, which will result in vibration of the pump’s casing.
Pump Impeller Imbalance: Impellers must be precisely balanced, as an imbalance of an impeller can cause an increase in 1X vibration.
Misaligned Shaft: Misalignment comes in various forms - axial misalignment, radial misalignment, and a combination of axial and radial misalignment. This makes the misaligned condition difficult to diagnose. Misalignment can cause an increase in structural support stiffness, which could decrease the vibration amplitude, especially at 1X. Whereas frequencies at 2X and 3X may increase due to the additional restraint at the bearings, caused by the misalignment. Overall, it’s difficult to predict what misalignment will do to the vibration amplitude because it can affect both the forces and the stiffnesses of the machine. Changes in the vibration monitoring signature are very helpful in identifying misalignment.
Choosing a Sensor for a Pump
The type of vibration sensor that is best for your pump depends on the type of pump being monitored and the frequencies of interest. There are, however, different monitoring methods that you can choose from to best meet your needs. Typically, with fluid film bearing machines, we’ll be using proximity probes to monitor vibration. With rolling element bearing (REB) machines, we will use casing mounted sensors that monitor either velocity or acceleration.
Rotor Related Frequencies: For most pumps with either fluid film bearings or rolling element bearings, a general vibration health monitoring range will be from 1/4X to 3X. This range is where the rotor related problems occur, namely unbalance, misalignment, rotor to stator rubs, instability, looseness, shaft crack, cage flaws, et cetera. It is important the vibration sensor chosen can cover these frequencies.
Bearing Related Frequencies: The bearing related frequencies are associated with rolling element bearings. They include the inner race element passage frequency, the outer race element passage frequency, and element spin frequency. The REB cage frequency is usually manifested close to 1/2X, so it would be found in the rotor related frequencies. For rolling element bearing, the fault frequencies, whether they be inner race, outer race, or ball spin, are going to be found in the bearing related region from 1 to 6 times the outer element race passage frequency. If the vibrational energy in this region increases 2 to 3 times baseline values, this is indicative of a bearing related problem. Typically, pumps that run at 60Hz or less, the frequency range is suitable for a velocity sensor or transmitter.
High-Frequency Monitoring: For REB machines that operate at greater than 60Hz, an accelerometer sensor or transmitter is used to measure machinery vibration. Typically, this provides a very good signal to noise ratio.
Learn more about various solutions for vibration monitoring of pumps from Metrix on our companion application page Vibration Monitoring of Pumps.
Summary
The above are general guidelines. By choosing the right sensor, depending upon the bearings and machine type, as well as the vibration frequencies of interest, you will obtain the early warnings necessary for predictive and proactive maintenance of your pump. If you have more specific questions, please reach out to us.
By Sarah Hildreth, Metrix Inside Sales Representative