When Control Systems Should Be Used as Vibration Protection Systems
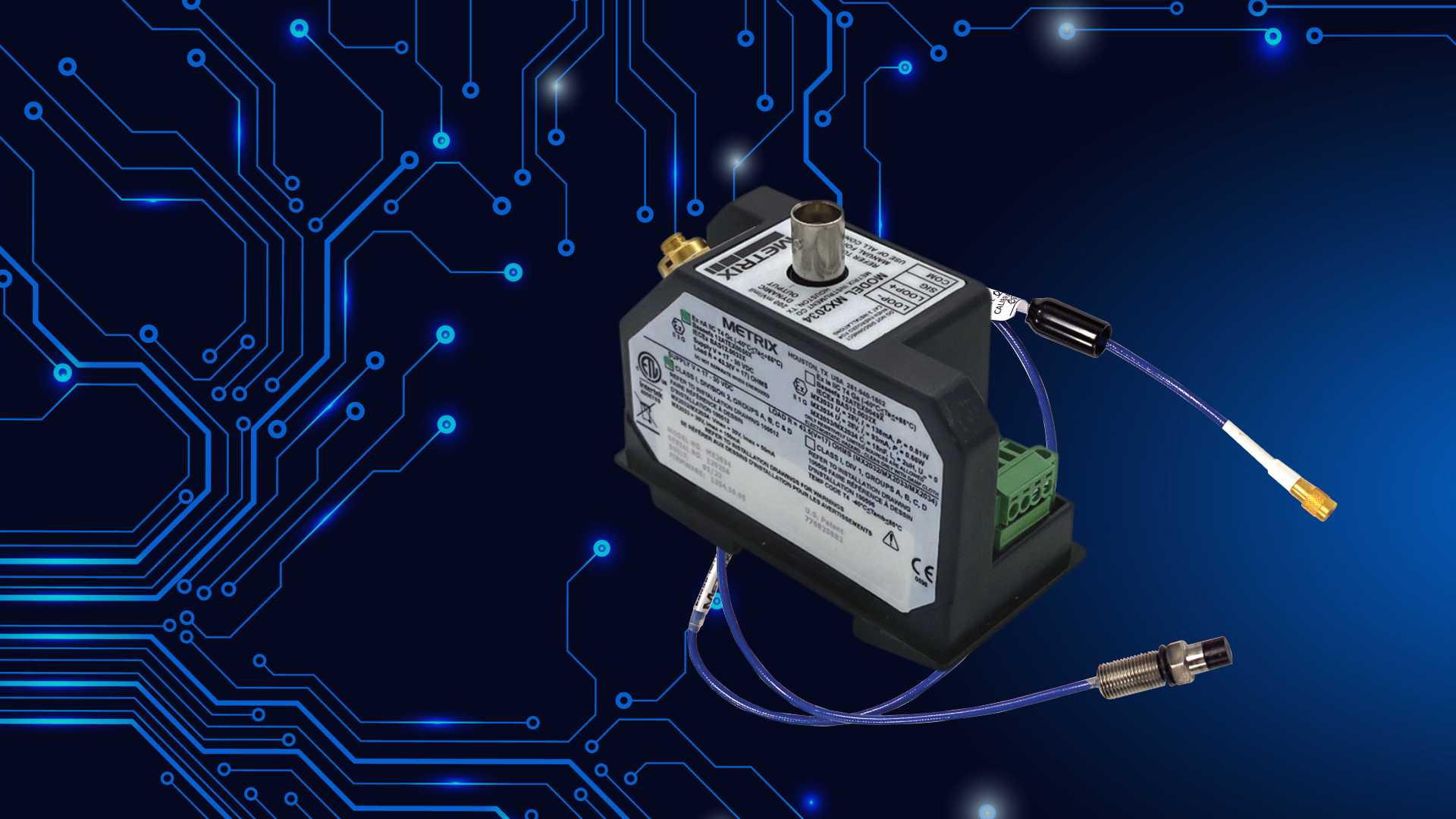
The MX2034 4-20 mA Proximity Transmitter and MX8030 Proximity Probe are essential when monitoring vibration
It’s often been said that a control system should not be used as a machinery protection system (MPS) or vibration monitoring system (VMS). The problem is the control system is often used as a machinery protection system. The machinery protection system is an added feature to the control system. You must have the control system to operate the plant. The control system takes on protective features for the machine and the process.
For example, low lube oil pressure, or loss of lube oil, can result in catastrophic failure of the machine. Lube oil pressure does not go to the vibration monitoring system, it is a direct input to the machinery control system. Likewise, for certain machinery processes, like overpressure or no flow conditions, the control system is the system that protects the machine. The machinery protection system for vibration is often waiting for an abnormal vibration event to occur, whereas the control system takes action while evaluating the input measurement parameters that may affect the machine.
The Argument
The argument used to be that the PLC (Programmable Logic Controller), DCS (Distributed Control System), or SCADA (Supervisory Control and Data Acquisition) System did not have the scan rate necessary for machinery protection for vibration and position sensors. That is simply no longer the case. Even though the scan speed is a key differentiator between DCSs and PLCs, either can now be adequately used for machinery vibration protection. PLCs are designed to meet the needs of applications that require scan rates of ten milliseconds or less (0.01 seconds or less). This allows them to accurately control motors and drives running at high speeds, and this is 10 times faster than many VMSs, certainly adequate for radial vibration and thrust monitoring.
Customers are changing from vibration monitoring systems to transmitter PLC / DCS / SCADA systems for their vibration monitoring needs for three reasons: cost, ease of implementation, and exception based machinery diagnostics.
The customers that are choosing the vibration transmitter route, even while using proximity probes, for early warning and protection, are doing so because it’s easier and it minimizes the amount of equipment that needs to be maintained at the plant. If the control system sees a change in the vibration level from the transmitter, it can take action to minimize the problem and protect the machine.
Unscheduled Downtime
The vibration monitoring solution should depend upon the cost of Unscheduled Downtime. The sensory solution employed on a machinery asset depends upon the probability of an unscheduled downtime event and the associated production losses that could ensue.
The point made by the question above is, why would you need an MPS or VMS, if the Control System can monitor the same parameters? Since you absolutely need the Control System, why not just monitor and protect the machine, the process, personnel, and the community with the Control System? Why pay twice for protecting the machinery asset when the Control System can provide adequate vibration protection?
When is an MPS or VMS Necessary?
The argument for an MPS or VMS is twofold:
- Discrete vibration parameters can be simultaneously monitored along with the direct vibration, and
- The plant asset can be connected to a Condition Monitoring System (CMS), possibly accessible via an Intranet.
These two reasons especially apply to machinery assets, usually with fluid film bearings, that are using proximity probes as their means of machinery vibration protection.
Discrete vibration parameters like gap voltage, 1X amplitude and phase, 2X amplitude and phase, nX amplitude and phase, and not 1X, all have value, but the time and effort to set these parameters up, and maintain them, to make them meaningful, is often not justified. In most cases these parameters are present in the MPS or VMS but are not used for shutdown signals. Only the direct amplitude is used, and it is fed to the Control System, like a vibration transmitter output. The means of getting the discrete vibration parameters into the Control System is not justified unless the parameters are maintained. Since, in most cases, the discrete parameters are not maintained, the expense for the MPS or VMS as an addition to the Control System is not justified.
An online CMS is very convenient for those machinery assets where in which the cost of Unscheduled Downtime is very high – we call these assets Critical Assets (without these assets the plant does not operate). Keep in mind, it is highly unlikely the plant has the human resource capacity to perform diagnostics on machines that have shown no change in vibration behavior. This is evident from the fact that no action is taken on the discrete vibration parameters discussed above. Why should the plant spend hours looking at vibration plots (dynamic data), when no change in vibration behavior has been noticed.
Conclusion
Metrix wants to provide early warning of a machine problem, so you can take action, and perform machinery diagnostics when you need to. Only on the most critical assets, is the MPS or VMS justified. The MPS or VMS is justified when you can take the time to evaluate and set limits upon the discrete vibration parameters like gap voltage, 1X amplitude and phase, 2X amplitude and phase, nX amplitude and phase, and not 1X, and that can only be afforded on critical assets.
This blog is intended to shed light on why more and more customers are choosing a transmitter vibration monitoring methodology in lieu of a permanently rack based vibration monitoring solution.
For more information, there are two whitepapers that may be useful. One is Metrix Vibration Monitoring Methodology and the other is Proper Use of Transmitters and Protection Systems. Please let us know if you have any questions or need help with your vibration monitoring solution.
By Everett Jesse, Vice President of Sales and Marketing