Resonance and Vibration | How Does Resonance Affect Vibration?
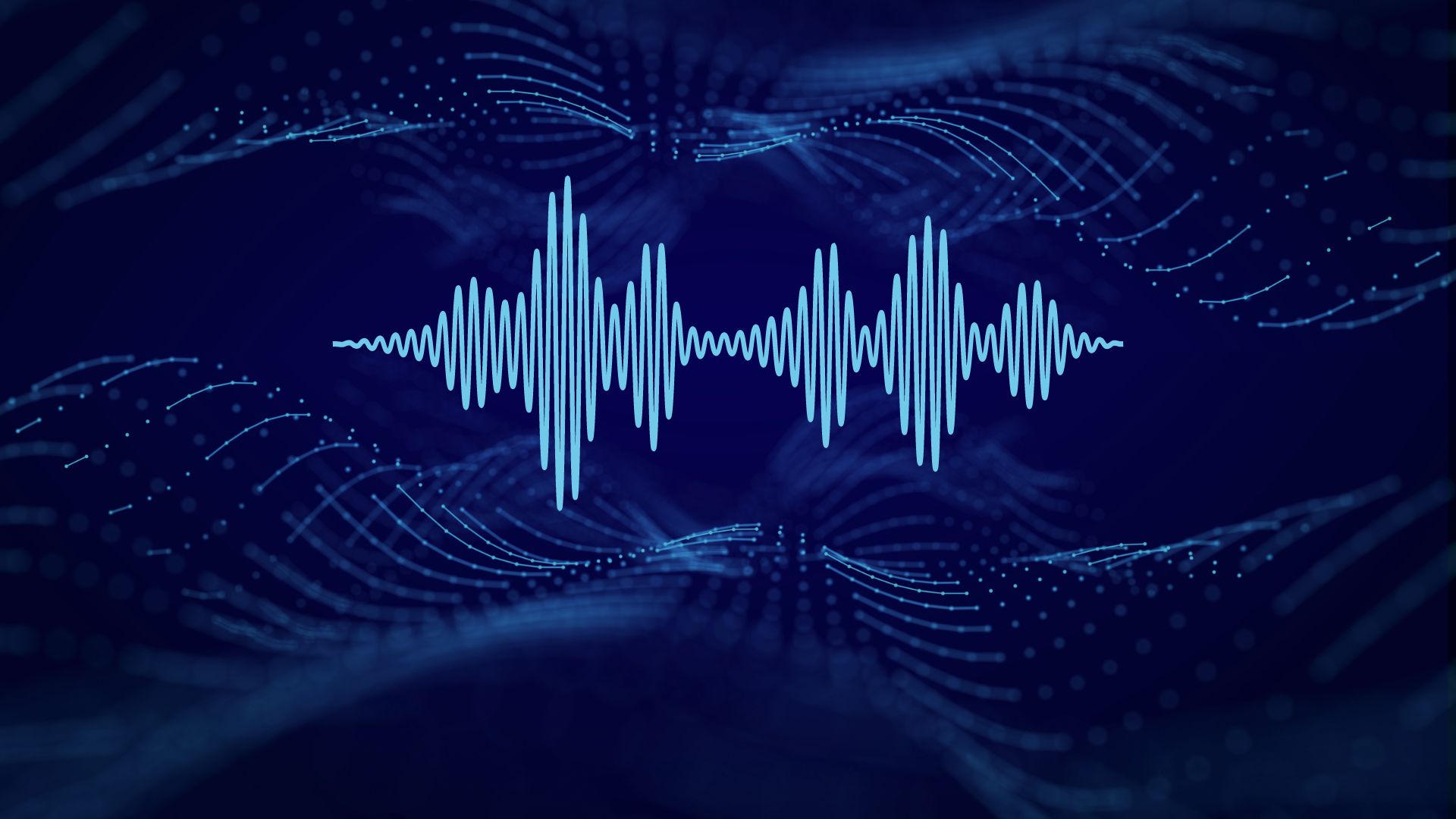
Resonance and vibration are closely linked
“Resonance can be the silent killer of any machine and supporting structure.”
-- Jack Difranco, Southeast United States Regional Sales Manager
Resonance and Vibration: Definitions, Relationships, Causes, and Effects
In industrial settings, resonance and vibration have proven far more dangerous than they might first appear. While the engineer may have assumed they accounted for these forces, it’s clear that it’s easy to underestimate how these seemingly small movements can land operators in major hot water. We’ll look at these concepts, the relationship between them, and what it ultimately means for your machinery assets.
It is important to understand that every machine and supporting structure in your plant will have a natural frequency or frequencies. Mass and Stiffness will determine the resonant frequencies within the machine and the supporting structures.
So, what is resonance? Oscillating forces causing a machine or structure to vibrate at its natural frequency.
Resonance can also be considered the excitation of a natural frequency.
Any source of vibration can produce resonance if it coincides with the natural frequency of the object:
1. On a machine startup or shutdown, the unbalanced force can excite natural frequencies that may exist at or below the machine’s running speed.
2. As bearings wear, the stiffness of the system changes, which could result in the natural frequency changing and then coinciding with one of the machine’s forcing functions, resulting in resonance.
3. If a rotor (shaft) is misaligned, or has a crack, it will change the system’s stiffness, which will change the natural frequency. If the natural frequency coincides with one of the machine’s forcing functions (e.g. unbalance force, blade passage rate, gear meshing forces, etc.), this will result in resonance.
4. The structure supporting the machine can also affect the stiffness of the machine system. If the structure is not adequate, or starts to breakdown (e.g., rust, bolts coming loose, concrete or structure cracking, etc.), the system stiffness will change, which could result in resonance.
A Deeper Look at Resonance
When we refer to resonance, we’re referring to how an object or system is affected by an oscillating force at the system’s natural frequency. In this case, the systems are the rotating or reciprocating machines within your plant. Mechanical resonance is often the missing link when you’re wondering why careful balancing and alignment precautions have failed. Each object has its own natural frequencies at which they’re subject to resonant vibration, and it doesn’t always take much of a system change before you start seeing the effects of stronger vibrations.
It may seem logical to stay as far away from the natural frequencies of an object as possible, but this is difficult to achieve. Most machine designers try to keep the forcing functions of a machine (e.g., running speed, number of fan blades or impeller blades times running speed, gear mesh frequencies, etc.) stay at least 20 percent away from the natural frequencies of the machine. As you approach the natural frequency, whatever it happens to be, even the tiniest, unexpected shift in forcing function or stiffness can cause the machine to go into resonance. The 20 percent rule is used because the natural frequencies can have a wide range, depending on the stiffness of the system, and how the system stiffness can change in time (e.g., bearing wear, lubrication changes, alignment changes, structural changes, etc.).
A common understanding: If you have ever been singing in the shower and hit a note that is louder than the others, you have just found the natural frequency of your shower. Or better, tune a guitar string and pluck it over and over and you will get the same sound. That is the natural frequency of the string.
Resonance and Vibration
Oscillations have a way of sneaking up on people, particularly when one movement is compounded by another. This is why you might see a bridge close just a few weeks (or even days) after construction. The structure might be designed to hold 2,000 people with calculated environmental conditions (under calculating maximum winds and thermal cycles) but the combined force of movement from all the pedestrians may cause it to start wobbling when just 1,000 are on it. That is why Army units are not allowed to walk in step while crossing a bridge, they can create a forcing function, which coincides with the natural frequency of the bridge that can lead to the bridge’s failure.
How does resonance affect vibration? Machinery vibration is a ratio of forces to stiffnesses. Either the changes in forces, or the changes in stiffnesses, can affect the vibration amplitude. If the vibration frequency coincides with the natural frequency of the machine, only the damping inherent in the machine (structure) will constrain the amplitude of vibration. In fluid film bearing machines, the damping stiffness comes from the fluid wedge that is developed in the bearings supporting the rotor. The fluid wedge acts as a shock absorber, dampening the vibration. In rolling element bearing machines, the fluid wedge on each of the rolling elements is typically not sufficient to provide adequate dampening. That is why most rolling element bearing machines operate less than their natural frequency (first balance resonance), following the 20 percent rule mentioned above.
The Problem of Frequency
What is the difference between resonance and vibration? It is not that there is a difference between resonance and vibration, rather than resonance occurs when the forcing function (vibration) of the machine coincides with the natural frequency of the machine, and the only restraint in the system, is damping. So, resonance is a special form of vibration, where the vibration is equal to the natural frequency of the machine. The natural frequency being defined by the square root of the ratio system stiffness divided by system mass. Resonance can result in system failure, that is why it should be avoided.
The engineers on the bridge could certainly picture the bridge withstanding the physical mass of pedestrians, but what is difficult to predict is if the people are walking or running in step. Likewise, in a machine, the forcing functions are predicted to avoid natural frequencies. Sometimes those natural frequencies can change, making them difficult to predict.
Avoiding Resonance in Rotating and Reciprocating Machines
Industrial settings can be rife with resonance, and unfortunately, the force is easily misdiagnosed as a mass imbalance when it’s really a change in system stiffness. If you want to avoid resonance, here are a few tips:
● Adjust the natural frequency: As discussed, natural frequencies have ranges, and there are times when you can change them. Adding stiffeners and or lowering mass, can increase the natural frequency. Likewise, reducing stiffness and increasing mass, can lower the natural frequency. Depending on the machine’s running speed, one has to determine what is the best way to move the natural frequency away from the running speed.
● During startup and shutdown, pass through the resonant frequency as quickly as possible, don’t dwell on the natural frequency.
● Add dampers: The purpose of a damper is to increase the damping of the overall system. When resonance occurs, the increase in damping reduces the amplitude of the vibration. You might have a few options if you want to implement this solution, and it’s important to account for the absorption strength of each potential system. This solution is likely the best strategy if you’re working with a machine that has a very stable speed.
These tips may sound simple in theory, but they’re rarely easy to implement in practice. Any variability can work against even the best-laid plans. For instance, adding mass to a structure, may lower the natural frequency, but it also increases the load on the structure. To compensate for the increased load, one may add a support to increase the stiffness, which increases the natural frequency, which is the opposite of what you want to accomplish. Careful consideration needs to be made when making any change to the machinery system.
Note: The machinery skids produced by various manufacturers, are designed to ensure resonance issues don’t occur. However, when the machinery skid is landed and attached to the Earth, the resonance frequencies can possibly change. Care must be taken on startup and shutdowns, and at running speed to ensure there are no abnormal resonances, which can impact the machine.
If a machine is operating within 15 percent of the natural frequency, it can amplify the vibration as much as 2 to 5 times or more, which can be detrimental to the machine. In these situations, resonance can damage machines and supporting structures, for example:
1. Broken bolts in supporting structures,
2. Broken welds in supporting structures,
3. Broken or loose foundation concrete, and
4. Premature bearing wear.
5. Increased vibration in general, resulting in excessive noise, reduced product quality and ultimately on-stream performance.
It is crucial to have the proper vibration monitoring system to prevent unnecessary damage and expensive repairs or replacement of your machines. Our goal at Metrix Vibration is to ensure your on-stream performance and quality of your products is achieved year over year.
The Metrix Promise
We have an extensive team of engineers with years of experience to assist you in selecting the proper vibration monitoring system. If you're looking for affordable options to protect your machines, we offer a variety of equipment, including switches, sensors, and transmitters, so you have a way to monitor vibration, especially those at resonant frequencies.
By Jack Difranco, Southeast United States Regional Sales Manager