The Advantages of Digital Proximity Systems for Vibration Monitoring
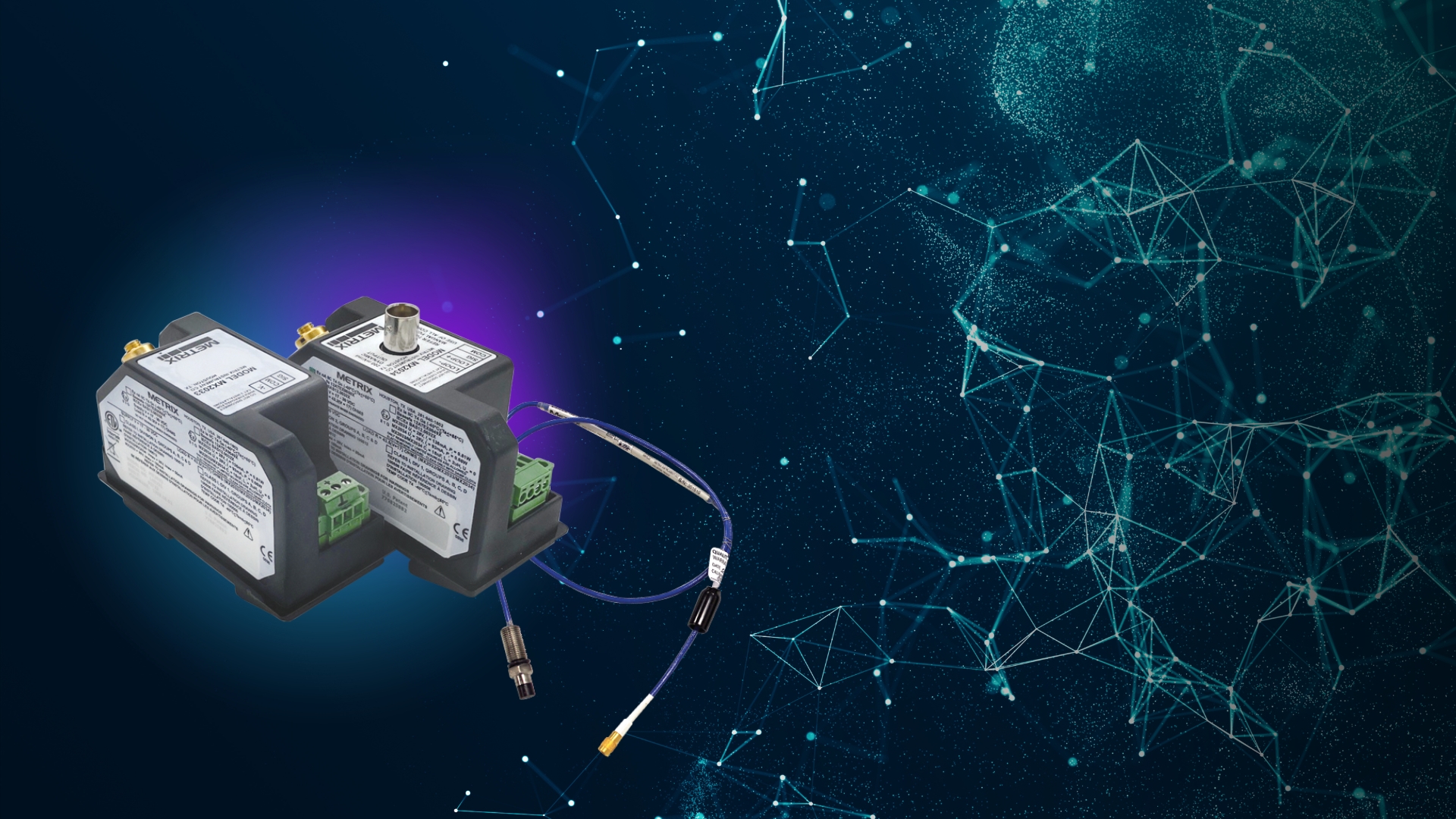
The MX2033 3-Wire Driver and MX2034 4-20 mA Transmitter are a part of the Metrix Digital Proximity System
Don Bently invented the proximity system that measures rotor vibration and position in the late 1950’s. The eddy current proximity probe system was ideal for monitoring machines with fluid film bearings without contacting the vibrating shaft. The concept of shaft monitoring for fluid film bearing machines was not new, shaft riders, basically spring-loaded plungers that contacted the shaft and incorporated an accelerometer at the opposite end, had been providing vibratory information for decades. With the advent of the personal computer in the late 1970’s, and the digital age that followed, it was natural to start thinking of how the proximity system would change in the future. One could visualize a world in which a machinery technician or engineer would want to change the configuration of a proximity system to fit their current need, and they would just need to connect to the oscillator demodulator and configure it for material type, system length and probe type. Sort of like a universal spare part. Well, Mr. Bently did think of that and patented the first digital proximity system in 1993. Bently did not commercialize it due to the slow computer processors at the time. The processors were not able to overcome analog systems, that didn’t occur until 2012. In 2005 Metrix produced the first commercially viable digital proximity system, the TXR and TXA, however, they weren’t ready for high-speed turbo machinery. In 2012 Metrix created the Digital Proximity System (DPS), and then in 2016 Metrix fulfilled on the vision to create a field configurable DPS, which became the universal spare part for the proximity measurement industry today. There are now tens of thousands of DPS units in operation around the world.
How It Works
The DPS converts an analog proximity signal input, into a digital signal, and then provides an analog signal output, usually at 200 mV/mil (7.87 mV/µm). The digital conversion in the middle, as well as the analog output, was made possible by having a CPU (Central Processing Unit) that had the amplitude and frequency resolution better than a purely analog proximity system. This digital conversion in the middle made possible the vision to create an API 670 compliant sensor that could be configured in the field for material type, system length and probe type. The DPS versatility is allowing technicians and engineers to be more efficient in their jobs, and purchasing managers to reduce spare part inventories, saving industrial plants money.
The DPS Provides Input to Vibration Monitoring Systems or Control Systems
A digital proximity driver or transmitter is available, depending on the required signal output format: the MX2033 3-Wire Driver is used with monitoring systems and the MX2034 4-20 mA Transmitter is used with control systems. There is also an MX2034 4-wire version that can supply both the dynamic signal to a monitoring system and the 4-20 mA signal to a control system. These models are fully compatible with a large variety of probes and cables from Metrix, BN, and other manufacturers.
The MX2033 Driver’s dynamic voltage output (mV/μm or mV/mil) is compatible with industry-standard continuous vibration monitoring systems and is in the format specified in API Standard 670. It uses -24Vdc excitation and provides the output signal in mV/μm or mV/mil, typically 7.87 mV/μm or 200mV/mil respectively.
The MX2034 4-20 mA Transmitter current output (mA/µm or mA/mil) provides thrust, radial vibration, or shaft speed measurements directly to Programmable Logic Controllers (PLC), Distributed Control Systems (DCS) and Supervisory Control and Data Acquisition (SCADA) systems, or other instrumentation that accepts an ISA Standard 4-20 mA signal, without the use of a separate monitoring system. The transmitter is a +24 Vdc current loop powered device, that provides a scaled output proportional to position, vibration or speed. The unique feature of this device is that it can be changed in the field depending upon the output you need.
A proximity system is perfect for complex fluid film bearing measurement situations, whether it be for high speed integrally geared compressor or slow speed pumps. If the machine has fluid film bearings, Metrix can help you with a solution that makes economic sense given the cost of unscheduled downtime. The vibration monitoring solution chosen for your application should depend upon the cost of unscheduled downtime. Unscheduled downtime, caused by a problem coming from a rotating or reciprocating machine, is the costliest downtime for a plant. The plant loses money from lost profits (Lost Opportunity Cost = loss of profitable output), expedited repair, material and labor costs, standby labor costs, quality issues, customer trust / delivery issues, and most importantly personnel safety concerns. The sensory solution employed on a machinery asset depends upon the probability of an unscheduled downtime event. If the asset downtime does not present a major risk to personnel, the facility or community, then the vibration monitoring solution is reduced (see Metrix Application Note “Monitoring Methodology” for more detail), usually a proximity transmitter-based solution is the best choice. If the machine is critical, high Lost Opportunity Costs due to unscheduled downtime, then a proximity driver going to a monitoring system is a better choice.
Change the Factory Ordered Configuration in the Field
One of the main reasons people buy the Metrix DPS is the ease at which one can reconfigure the unit to suit your needs. This is easily done using the Change Configuration Menu in the DPS software. The menu is displayed by clicking on the “Change Configuration” button. Depending upon what device is connected will determine what menu features are active, below is the Change Configuration Menu for a MX2033 Driver:
The Change Configuration Menu for the MX2034 Transmitter is similar, but has added fields due to its increased functionality:
Each of the features of the Change Configuration Menu will be described below. Please note – upon making any changes to the DPS Unit be sure to conduct a verification check to ensure the proximity probe system (probe, cable and DPS Unit) is within required tolerances. The Metrix 9060 Series of Static Calibrators can be used for these system checks.
Device Type - will either be the MX2033 Driver or MX2034 Transmitter as appropriate to the Connected Device or the Simulated Mode.
Configuration Type – will use a Standard characteristic (linear curve) or a Custom characteristic from a Custom Calibration defined linear curve. If “Custom” is chosen the “Send Configuration” button is changed to a “Next” button, that will take the user to a Verification Screen to generate the Custom Characteristic (linear curve).
Measurement – is used for a MX2034 Transmitter. For a MX2033 Driver this feature is not necessary because the measurement is made in the Monitoring System. For the Transmitter it can be configured for position, vibration or for speed.
Probe Series – This allows the software to choose the appropriate linear characteristic based on the probe type, in combination with the target material, probe tip diameter, and system length. The most flexibility in the system is using probe series MX8030 and MX2030, the other probe series are limited to AISI 4140 Steel, and typical system lengths of 5, 7 and 9 meters. There are some exceptions like the BN and Metrix 3000 Series which only had lengths of 15 and 20 feet. This is also where you find the MX8030 TIGHTVIEW® selection.
Target Material – This menu allows one to change the target material from AISI 4140 Carbon Steel to another shaft material. Only Metrix Probe Series MX8030 and MX2030 allows the user to change to the available materials listed. The materials listed represented 95% of the material types ever ordered from Metrix. If you do not see a material that you need, Metrix can add the material to the software upon request along with a small engineering fee. If you have a BN 3300XL Series Probe and you need a different material type other than 4140 you can configure the DPS Unit with the MX8030, select the proper material type, and you will achieve satisfactory results.
Probe Tip Diameter – Probe Tip Diameter selection depends upon the Probe Series. Most probes are 5mm/8mm, some probes like the Metrix 7200 and BN 3300XL also have 11mm probe tips. The 3000 Series probes have 0.19 inch and 0.30 inch diameter tips.
System Length – this feature allows the user to switch between standard system lengths for the Probe Series selected. For example, the Metrix 7200 and BN 3300XL has 5 and 9 meter System Lengths listed. The Metrix MX8030 and MX2030 Probe Series allow the DPS to take advantage of extended Systems Lengths from 1 to 12 meters for Vibration, and to 20 meters for Speed and Thrust measurements. Typical System Lengths for MX8030 and MX2030 are 5, 7, and 9 meter systems. If a user wants to use a length other than listed, like 7.6 meters, the user would use a 7 meter or an 8 meter System Length and perform a verification check to determine which length provided the best results. If the verification is not within limits a Custom Calibration can be conducted using the Verification Voltage values. Users can use the Metrix MX8020-001 Cable Trimming and Connector Kit to alter the length of a MX8030 probe or MX8031 extension cable. Users no longer have to keep coils of extension cable in their junction boxes.
Full Scale Range – this feature is dependent upon what is selected for the MX2034 Transmitter measurement. The MX2033 Driver output goes to a monitoring system, so the Full-Scale Range is not used. If the Transmitter Measurement was Position, then the 4 to 20 milliamp scale can be selected for the appropriate displacement output, either in mils or microns (µm). If the Transmitter Measurement was Vibration then the 4 to 20 milliamp scale can be selected for the appropriate vibration output, either in mils pk-pk (peak to peak) or microns pk-pk. If the Transmitter Measurement was Speed, then the 4 to 20 milliamp scale can be selected for the appropriate speed output in rpm (revolutions per minute). Extended Range – This feature is used to extend an MX8030/MX2030 probe from a 10 to 90 mil (250 to 2250 µm) linear range to a 20 to 180 mil (500 to 4500 µm) linear range, simply by changing the Scale Factor Range. When using the Extended Range feature the Incremental Scale Factor (ISF) is changed from 200 mV/mil (7.87 mV/µm) to 100 mV/mil (3.93 mV/um). Note: If one changes the configuration from factory, one must perform the Tuning and Calibration Steps.
Events/Rev – This stands for Events per Revolution. This applies when the MX2034 Transmitter is used as a Speed Transmitter. This is the number of pulses the phase trigger (speed) sensor is going to see for each revolution of the shaft. The number of pulses allowed depends upon the speed of the machine. The higher the speed, the less pulses per turn of the rotor are allowed. A maximum of 400,000 pulses per minute are allowed.
The Perfect Spare Part
Imagine being able to support a multitude of cable lengths, target materials and older probe systems with just a single driver or transmitter. Our Digital Proximity System (DPS) combines the performance of a fully API 670 compliant eddy-current proximity measurement system with the flexibility of digital configurability. The DPS was designed to fully comply with API 670 for linear range, interchangeability, standard probe mechanical configurations and other
details.
The DPS reduces the requirements for spare parts by allowing a single type of driver or transmitter to be field configured for a wide range of probe types, cable lengths and target materials including 8mm ceramic and 11mm probe tips.
The MX8030 triaxial probes and MX8031 triaxial extension cables with VIBELOCK® connectors, as well as MX2030 probes and MX2031 extension cables, are fully interchangeable with BN 3300 and 3300XL 5mm/8mm probe systems. This compatibility provides greater choice of suppliers without the need to replace installed probes, cables and drivers or transmitters.
If you have any questions about the Metrix Digital Proximity System, please don’t hesitate to give us a call.