Monitoring Your Reciprocating Compressor
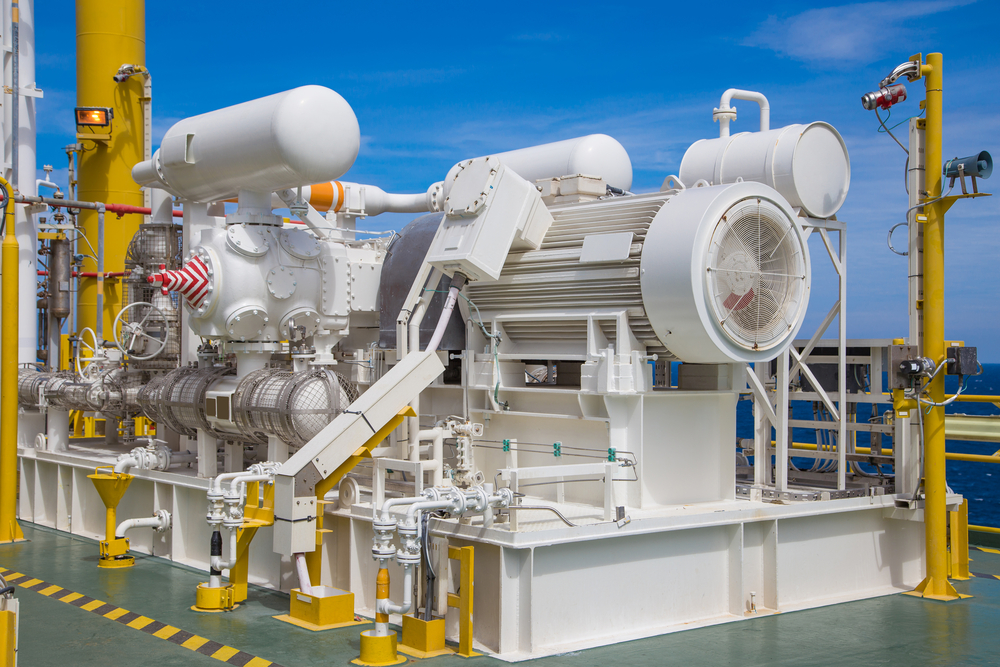
Reciprocating compressors are an integral part of many industrial processes
A reciprocating compressor is an important machine many industries rely on. These machines are essential for industries that deal with compressed gasses for pipelines, refineries, chemical plants and air separation units. As with most machinery, it is important that you properly care for your reciprocating compressors to ensure that they are running safely and efficiently. Depending upon the criticality of the machine the monitoring suite changes, this helps to ensure a return on your investment for the monitoring system.
Reciprocating Compressor Uses
Reciprocating compressors are found at a variety of industrial sites, as they are the most common type of air or gas compressor systems used. These machines are used to compress multiple types of gasses. They are an integral part of many industrial processes, including oil refining, chemical production and processing, gas processing and pipeline transport, and more.
A reciprocating compressor is considered a positive displacement compressor, utilizing both cylinders and pistons to provide its main function. First, gasses are fed into the compression cylinders. The pistons are then driven in a reciprocating motion, which compresses the gas and builds up pressure. Once the compression process is complete, the gas is then released out of the compressor into the next cylinder, or the next process, or a pipeline.
Types of Reciprocating Compressors
Reciprocating compressor uses span multiple industries. You are likely to find a reciprocating compressor at nearly any industrial site you may visit. Despite the many applications of reciprocating compressors across multiple industries, most compressors fall into one of two categories.
1. Single Acting Compressors - The first type of reciprocating compressor is a single-acting compressor. These compressors tend to be smaller and easier to manage. They boast moderate power but are best suited to circumstances where they do not need to run constantly. The smaller size of a single-acting reciprocating compressor means that it is also much more portable and more easily installed. These units do tend to run somewhat louder than other types of compressors, so that is also something to take into consideration if you are looking to add a reciprocating compressor to your site.
2. Double Acting Compressors - The other type of reciprocating compressor is the double-acting reciprocating compressor. As the name suggests, this reciprocating compressor utilizes both ends of each piston to compress air or other gasses (e.g. natural gas, CO2, H2, etc.). They do, however, work more efficiently than the single-acting reciprocating compressor.
In either case, choosing the right monitoring system depending upon the service of the reciprocating compressor is important. Where the process losses in a day can add up to hundreds of thousands of dollars, it is important to ensure that you have the tools to succeed. For smaller load applications, companies may only need a compressor on an occasional or moderate basis – a single-acting reciprocating compressor may suffice. If you have a larger operation with daily or constant needs, a double-acting compressor might be the best option for you
Vibration Monitoring of Reciprocating Compressors
Regardless of the size of your compressor and the frequency of use, it is essential that your reciprocating compressor is receiving the proper maintenance and care. A condition-based approach to maintenance has proven to be the most cost-effective way to maintain a rotating and or reciprocating asset (see Metrix Vibration Monitoring Methodology).
You can divide Reciprocating Compressor Monitoring into three classifications -
1. Balance of Plant machines usually have a monthly portable data collection process to trend vibration levels
2. Essential machines usually have a sensor suite that reports crankcase vibration, impact monitoring at each crosshead and rod drop monitoring for each cylinder to measure rider band wear
3. Critical machines where they have everything monitored in Essential machines and the ability to look at cylinder pressure versus volume (PV) curves and valve temperature
Balance of Plant machines impact less than 10% of the process, Essential machines have the ability to impact up to 25% of the process, and Critical machines can impact 25% or more of the process. These percentages are typical and can change depending upon the total cost of one day of unscheduled downtime. Total cost of downtime includes the maintenance spend as well as the lost production losses due to not operating.
Besides vibration monitoring, monitoring temperatures and conducting routine required maintenance will help your reciprocating compressor last its design lifetime.
Monitor Temperatures
Monitoring inlet and outlet temperature of the reciprocating compressor can be helpful to determine if flow through the machine is normal. An abnormal change in differential temperature may indicate valve line up issues or cylinder inlet and outlet valve issues. If there is a sudden temperature increase while the machine is running, that often indicates an imminent problem within the system. At that point, you should stop and inspect the machine to prevent failure.
Regular Required Maintenance
Remember to keep up with the maintenance that is recommended by the manufacturer. Depending on the size and function of your reciprocating compressor, there will be a list of specific things you do to guarantee that it runs for its design lifetime. This may include maintaining consistent lubricant levels, checking for wear and tear on the machine, and keeping the compressor and its surrounding area clean.
Let the Experts Help
For more information about how vibration monitoring systems can alert you to changes within your reciprocating compressor, prevent costly downtime, and preserve the integrity of your machine, contact Metrix Vibration today.
By Vivek Joshi, Country Manager - India