How to Choose Vibration Sensors or Transmitters for Rotating or Reciprocating Equipment?
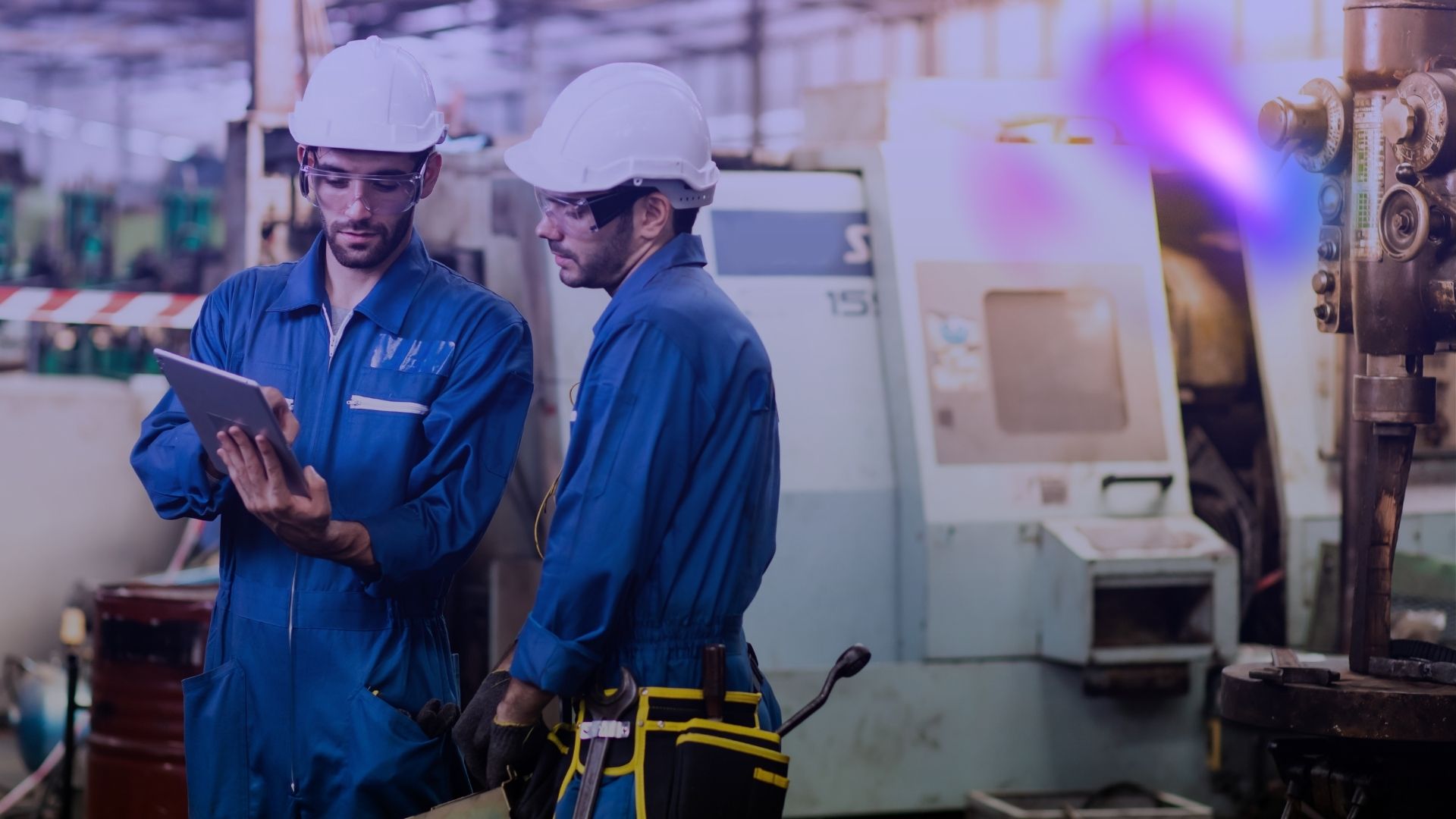
Monitoring the health of your rotating and reciprocating machinery assets is essential for many industries
Many industries rely on different types of rotating and reciprocating machinery for their processes to work correctly, and to ensure timely and safe operations. Operators must ensure their equipment is functioning appropriately, so that production remains on schedule. Vibrations of rotary equipment like pumps, fans, cooling towers, blowers, motors, and other equipment should be monitored. An effective monitoring device for such assets is a vibration sensor (usually a voltage output) or a transmitter (4-20mA output) that monitors vibration output from the machine. The type of sensor or transmitter can be selected according to the machine speed and bearing type.
The various criteria to consider when selecting a sensor or transmitter are - the type of machine, the bearing type (either rolling element or fluid film), the frequency range, and the accessibility of sensor locations. The vibration sensor or transmitter should be chosen according to the environmental influences (e.g. temperature, space constraints, moisture, hazardous area, etc.) of the place where it is installed. If we are monitoring fluid film bearing machines, the characteristics of the surface of the machine where the proximity sensor is used, also needs to be considered. Vibration sensors are used for monitoring systems, whereas vibration transmitters are used for control system inputs. In this blog post, we will be discussing sensors, but it also applies to vibration transmitters.
Vibration Sensors Sense Vibratory Motion
A vibration sensor is a device that measures the vibration characteristics in a machine, system, or piece of equipment. The data gathered from the sensor is the vibration frequency, amplitude, phase angle and the form of the vibration. These vibration sensors collect information and determine the vibration output that indicates whether or not the machine is running at normal levels. The vibration signal can show unbalance, misalignment, lubrication problems, or other issues that can lead to machine breakdown. If a problem occurs in the machine, it will usually show up in the vibration signature. The trend of the vibration value of the machine provides insight into the machine condition. By measuring vibration and looking for changes, you can spot problems early and take action before they become bigger problems. This is called preventive maintenance.
Why Do You Need Vibration Monitoring Equipment?
There are many benefits to implementing machine vibration monitoring, including:
Monitor Repair Needs
When the vibration sensor is connected to a machine, you can track the vibration data in real-time and get notified of changing levels of vibration. This helps with predictive maintenance, giving you valuable information about when to perform repair work on the asset monitored by the vibration sensor.
Understanding the Cause of Damage
Vibration analysis can show valuable data that helps with root cause analysis (RCA). By checking the vibration results, you can find the source of any vibrations that indicate a fault and prevent subsequent damage.
Maintain an Overall Health Check on Equipment
Condition monitoring of your equipment heavily relies on sensors, especially vibration sensors. The data collected from these sensors allows valuable insight into the machine without taking the machine apart. It can also show important information on the functionality of your system if you are trying to change or update your working processes.
What are the Types of Vibration Sensors?
There are many different types of vibration sensors, each tailored to best fit the machinery application they’re intended for. Though these sensors are used in many industries, including oil and gas pipelines, refineries, chemical plants, power generation, water and wastewater, and other industrial processes, there are three main types of vibration sensors.
Accelerometers
The most common types of vibration sensors are accelerometers. They measure the change in acceleration of the object they’re mounted on. This includes rotating and reciprocating machinery. If the sensor detects a change in velocity over time, the accelerometer will produce an electrical signal. The three types of accelerometers are piezoelectric, piezoresistive and MEMS (Microelectromechanical Systems). They work best for gear and rolling element bearing fault detection, or almost any faults in the mid to high-frequency range (>2000 Hz). They are also effective for detecting misalignment, unbalance, loose or broken parts, bent shafts, and component resonances. They have long life expectancies and a large frequency range.
For machines that operate at greater than 60 Hz, an accelerometer is generally used due to the possible high frequency content caused by gears or rolling element bearings. When talking about the vibration amplitude using acceleration, we use g’s or m/sec² RMS or g’s or m/sec² PK.
Figure 1: Vibration Waveform
Velocity Sensors
Velocity sensors measure the change in distance over time — the output of the sensor increases as the vibration amplitude increases. Velocity sensors are excellent for general vibration measurement and monitoring of reciprocating and rotating machinery. They are also easy to install because they are not sensitive to the surface they are mounted on. They are most commonly used for medium-frequency measurements (5 Hz to 2000 Hz) and provide a good temperature range. Some velocity sensors are electromechanical devices; they generate their signal and do not require an external power supply. Velocity sensors are usually used with rolling element bearing machines operating at ≤ 60 Hz (3600 rpm). When talking about the vibration amplitude using velocity, we use inches per second (ips) or mm/sec RMS or ips or mm/sec PK.
Displacement Sensors (aka Proximity Sensors)
Displacement sensors are non-contact sensors that produce a radio frequency magnetic field used to detect the relative movement between the probe tip and the metallic surface of a given object. They measure displacement directly and are typically used to monitor internal clearances and shaft motion.
These sensors work especially well for monitoring machines with fluid film bearings, either axial or radial bearings. They have excellent signal strength at low frequencies and are known for being reliable for monitoring and protecting turbo machinery with fluid film bearings, regardless of speed. They are particularly sensitive to surface material conditions and composition, so care should be taken in ensuring the target area the proximity probe is looking at is clean of surface imperfections. When talking about the vibration amplitude using proximity sensors, we use mils or microns PK-PK.
Talk to the Experts
Monitoring the health of your rotating and reciprocating machinery assets is essential for many industries. With proper vibration monitoring with vibration sensors or vibration transmitters, you’re able to obtain early warning of potential problems before they become big problems and affect the process or people. Though vibration sensors and transmitters provide essential information, it’s important to choose the right one for your needs. Contact the Metrix team today to begin that conversation.
By Sally Shim, Metrix Asia Regional Sales Manager