How to Use Accelerometers to Measure Vibration
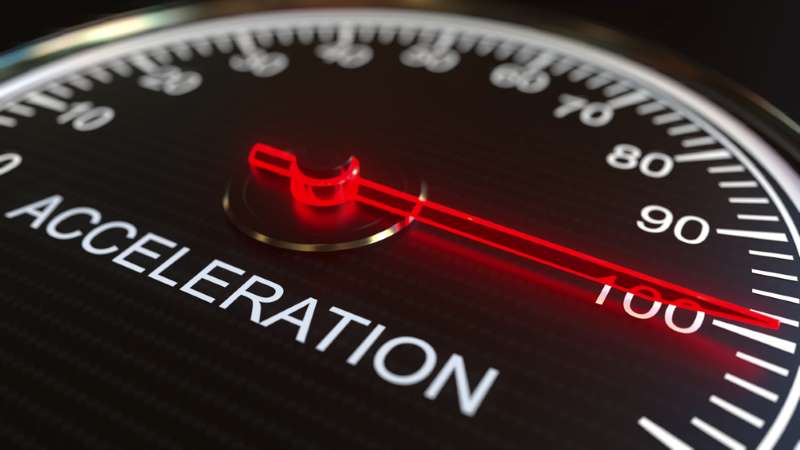
Wondering about accelerometers and how to use them?
Accelerometers are used to measure the acceleration of vibration of a given object. They can be used for anything from finding an object’s angle of tilt, by measuring the acceleration of gravity, to simply determining how fast an object is changing velocity. As accelerometers are easy to use and can operate across a broad range of frequencies, they are used for monitoring a wide variety of machines, including motors, pumps, fans, compressors, turbines and many other rotating and reciprocating machines across multiple industries.
What is an Accelerometer?
First, it is important to know that acceleration, when simply put, describes any change in velocity.
Thus, an accelerometer is a small electromechanical device that is used to measure acceleration as well as the different forces that are working on an object. Accelerometers can monitor both static and dynamic forces. Static forces, like gravity and friction, are forces that do not alter the direction or position of an object and remain uniform.
By contrast, dynamic forces do change the direction or position of an object and are not as predictable. Accelerometers are extremely useful because they detect changes in acceleration and convert them into vibration measurements. Accelerometers (acceleration sensors) measure vibration using electrical signals, which allow insights regarding the condition of a machine.
How Does an Accelerometer Work?
An accelerometer works by outputting an electronic signal from a sensor installed to measure dynamic or static acceleration. The type of sensor in the accelerometer will ultimately determine how the accelerometer itself reacts to acceleration.
For example, when acceleration is measured using a piezoelectric accelerometer, the interior of the piezoelectric sensor (crystal) is stressed. Stress, in turn, causes the sensor to generate an electrical charge proportional to the forces acting on the object. In this way, accelerometers sense when an object undergoes any sort of movement, measure the forces pushing on it, and output an electrical signal proportional to the acceleration sensed. This is true for MEMS accelerometers as well.
Accelerometer Sensors
As mentioned, accelerometer sensors can measure a variety of accelerations depending on the type. For these purposes, there are four main types of accelerometer sensors in use.
1. Piezoelectric Sensors
A piezoelectric accelerometer uses what is known as the piezoelectric effect, which is when an instrument produces an electrical charge after being put under stress. These sensors are much more sensitive than other types of accelerometers, such as piezoresistive accelerometers. Piezoelectric accelerometers are the most used sensors for measuring vibration and shock in industrial applications. A downside of these sensors is that they are AC coupled, meaning that they cannot measure static forces like gravity.
2. Piezoresistive Sensors
A piezoelectric accelerometer works by increasing its resistance in proportion to the forces that are acting upon it. Though they are less sensitive than piezoelectric accelerometers, piezoresistive devices have proven especially helpful in the auto industry. They are commonly used in vehicle test crashing to identify measurable quantities of force.
3. Capacitive Sensors
The most common type of accelerometer is the capacitive accelerometer. To figure out the acceleration of an object, capacitive sensors measure the alteration in electrical capacitance, which is the ability of an object to store energy in the form of an electrical charge. When a capacitive sensor detects acceleration, the sensor’s diaphragm begins to move, changing the distance between the capacitor plates inside. This helps to generate a reading of the acceleration that occurs.
4. Microelectromechanical Systems (MEMS)
A MEMS accelerometer operates on the nanoscale. Small changes in displacement between plates changes the capacitance, the change in capacitance is proportional to acceleration. Most commonly, MEMS are used in cell phones to determine how the cell phone is being held and oriented. When used in industrial settings to measure machine vibration they do the same thing, they can just take larger temperature extremes and have a broader frequency response range than in the cell phone application. In order to get the response range of a piezoelectric accelerometer MEMS accelerometers are often paired, one MEMS to capture low frequency <2000 Hz, and another MEMS to capture higher frequencies, >1000 Hz. The overlap is reconciled within the MEMS accelerometer assembly. MEMS accelerometers are often assembled in a triaxial arrangement to measure acceleration in three directions due to their compact size.
Accelerometers to Measure Vibration
Accelerometers measure vibration by monitoring acceleration and converting it into voltage. They are usually mounted on equipment to measure vibration on machines operating at greater than 60 Hz. On machines at 60 Hz or less an accelerometer integrated to velocity is usually used to identify any irregularities. A machine operating at or less than 60 Hz the integrated velocity signal has a better signal to noise ratio than a pure acceleration signal. When using an accelerometer to measure vibration, especially in an industrial setting, the ideal choice is most likely a piezoelectric accelerometer. Piezoelectric accelerometers can be categorized into two types — high impedance accelerometers and low impedance accelerometers.
High impedance piezoelectric accelerometers have a unique charge output that is converted into electrical voltage by a charge amplifier or impedance converter. In this kind of accelerometer, the electrical charge connects directly to the measurement instruments. Unlike low impedance accelerometers, high impedance accelerometers can be used in high-temperature situations.
Low impedance types use the same piezoelectric sensors as high impedance accelerometers but with a smaller built-in charge-to-voltage converter. They have low output noise and a wide frequency range compared to high impedance accelerometers. For this reason, low impedance accelerometers are more commonly found in industrial settings to help identify vibration issues within rotating and reciprocating machinery.
Why Monitor Vibration?
Vibration monitoring is a company’s best defense against unscheduled downtime. Unpredicted machine issues or failures can cost businesses time, money, and capital. By monitoring the vibration on your machinery, you can be alerted of any abnormal trends in your machine processes before the machine fails or critical damage occurs. Vibration monitoring systems can use various tools, from accelerometers to transmitters, to help record and share data, allowing you to run your machinery efficiently.
Finding the Right Accelerometer
Many different aspects go into choosing the right accelerometer for your needs. Depending on the characteristics you’re measuring and the machinery in question, you’ll need to consider many determining factors before making your choice.
At Metrix, we have been creating technology and services to help measure vibration and identify potential issues for many years. Whether you’re looking for a new acceleration vibration sensor that works for your machinery or simply need help with installation, we can help. To learn more about the vibration monitoring products we offer or to ask further questions about accelerometer technology, reach out today.