Proximity Monitoring for Machines - Touchless Detection of Issues
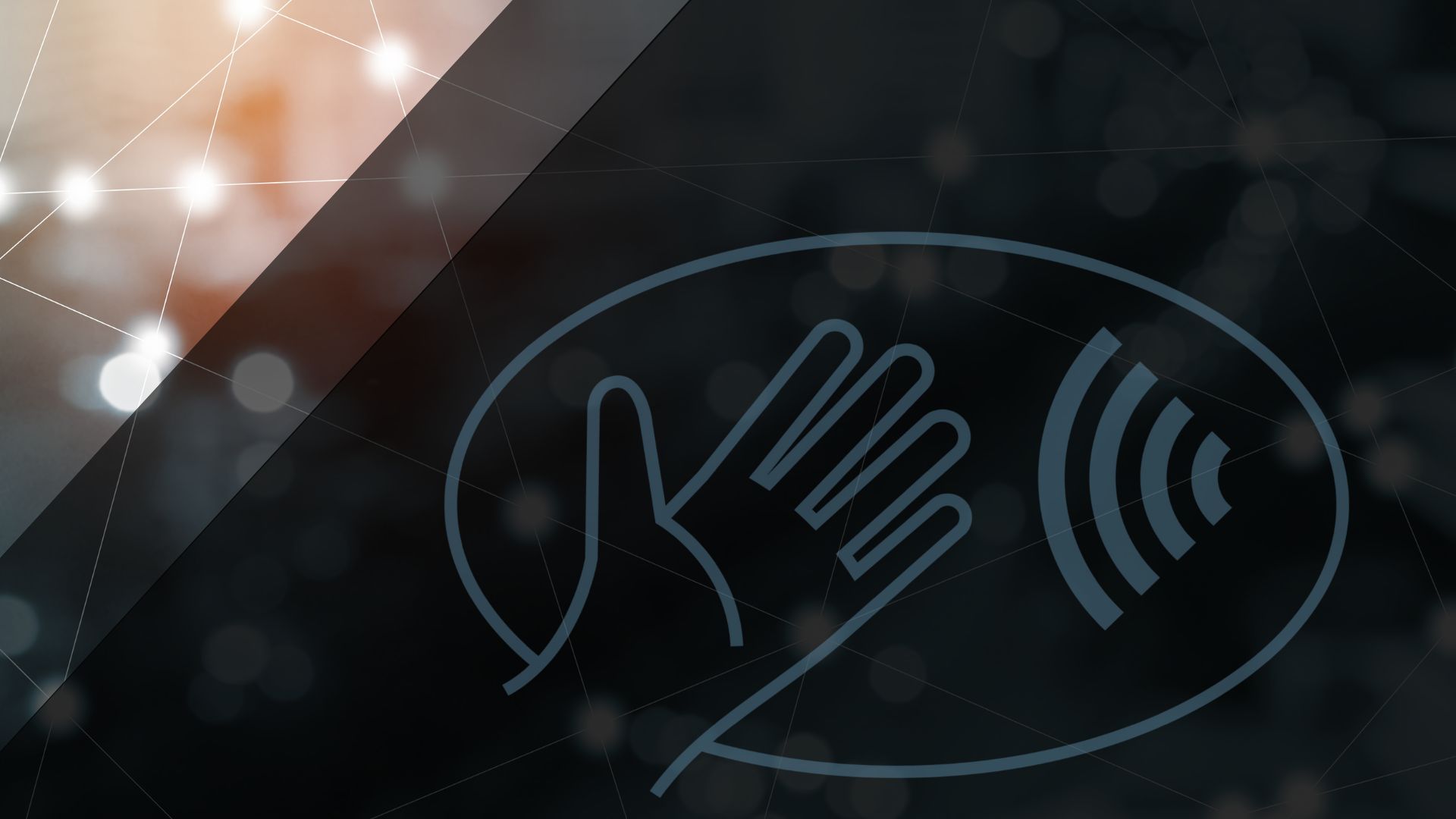
Proximity Monitoring for Machines with Touchless Detection
Proximity Probe Sensors Explained
When properly calibrated, a proximity sensor measures the linear distance from the probe tip to a nearby metallic surface. It is a non-contacting device which measures the displacement motion and position of an observed surface relative to the probe tip and probe mounting location. Proximity probes used for rotating and reciprocating machinery measurements usually operate on the eddy current principle and measure shaft displacement motion and position relative to the machine bearing(s) or housing. The physical distance in micrometers or mils between a target (e.g. a machinery shaft or piston rod) and a proximity probe tip is called the probe gap. Setting the probe gap refers to static (i.e. machine off) positioning of the probe to a distance from a metallic surface that is within the sensor’s linear range. This allows for linear electronic measurement of a movement (i.e. machine on) arising from dynamic radial vibration or changes in axial position about this static probe gap, provided it does not exceed the sensor system’s maximum linear range in either direction. Proximity probe sensors are known for their durability, reliability, and accuracy, and they are often used in harsh environments where physical contact with the object being sensed is not possible or desirable.
Proximity Sensors for Vibration Detection
One of the most effective implementations of non-contact proximity-based systems has been detecting vibration, and providing condition monitoring for motors, pumps, turbines, compressors and other high-value industrial equipment that utilize fluid film bearings. Small vibrations can serve as precursors to machine failure, which means early detection is critical for employee safety and your bottom line.
The concept of proximity monitoring for vibration is also fully scalable. Even the largest and most complex machines, to simple motor pump combinations, can be effectively monitored for problematic vibrations using an array of high-quality proximity probes. The relative motion between the shaft surface and the fluid film bearing surface is perfectly suited for a non-contacting eddy current generating proximity system.
How a Proximity Probe Sensor Works
A proximity probe sensor measures vibration by detecting changes in the electromagnetic field between the probe tip and the machine’s rotor surface, this is usually called probe gap. As the gap between the probe tip and the shaft surface changes, that movement can be sensed and reported as a change in vibration and/or position. Here's how it works:
1. Electromagnetic Field Generation: The proximity probe sensor generates an electromagnetic field and passes a high frequency alternating current through a coil inside the sensor's probe tip. This alternating radio frequency signal generates eddy currents in the surface of the metallic material.
2. Movement Detection: When a moving component, such as a rotating shaft or shaft surface enters the proximity probe's electromagnetic field, it creates eddy currents in the surface of the material, which changes the field strength.
3. Signal Processing: The proximity probe sensor measures these changes in the electromagnetic field and converts them into an electrical signal that can be sensed for both vibration and position.
4. Vibration Analysis: The electrical signal from the proximity probe sensor is then processed and analyzed to determine the frequency, amplitude, phase, and other characteristics of the vibration or position change.
By continuously monitoring the vibration of a machine, a proximity probe sensor can provide real-time information about the machine's health and help identify potential issues before they cause damage or failure. This allows for early detection of problems and timely maintenance to keep the machine running smoothly.
How are Eddy Current Probes Sensors Used for Monitoring Machine Condition?
Proximity probes are widely used for monitoring the condition of rotating and reciprocating machinery. They work by detecting changes in the electromagnetic field between the probe tip and the shaft surface, which can indicate changes in position, vibration, speed, or other characteristics of the machine's behavior. Here are some of the ways in which eddy current probes are used for machine condition monitoring:
1. Vibration Monitoring: Proximity probes are used to measure the vibration of rotating and reciprocating machinery with fluid film bearings, such as turbines, motors, pumps, or compressors. By measuring the displacement or movement of the shaft, they can detect changes in vibration that may indicate a fault in the machine such as unbalance or misalignment.
2. Runout and Eccentricity Measurement: Proximity probes can also be used to measure the runout or eccentricity (rotor bow) of rotating machinery components, such as shafts for motors, turbines, compressors and other machines. By detecting changes in the position of the target surface, they can provide information about the condition of the machine.
3. Speed: Proximity probes can measure high speed and low speed rotating shafts with multiple events per rotation by looking for an event/s and measuring how many times that event/s passes the probe per rotation. The Metrix system is currently able to provide accurate measurement up to 400,000 pulses per minute, making them perfect for high-speed machinery.
4. Phase Marker: A proximity probe can be used to create a once per turn pulse that can be used to measure the angle or direction of any vibration signal. The Phase Marker does this by measuring a known event, such as the probe looking at a notch on the rotating shaft, creating a Phase Marker. With this data, it’s possible to diagnose failures such as looseness, unbalance, rotor bow, misalignment, stater to rotor rubs, instability, resonance, shaft crack and other malfunctions.
Overall, eddy current proximity probes are a useful tool for machine condition monitoring because they can measure the relative movement between the probe tip and the shaft surface material or piston rod. Due to its non-contact nature, it can operate at a very wide speed range, and can provide accurate and sensitive measurements of position, vibration, and other machine characteristics.
For more information about building your own cutting-edge machine condition monitoring system, visit Metrix Vibration or contact us with any questions.