Seismic Monitoring: Vibration Detection of Machine Condition
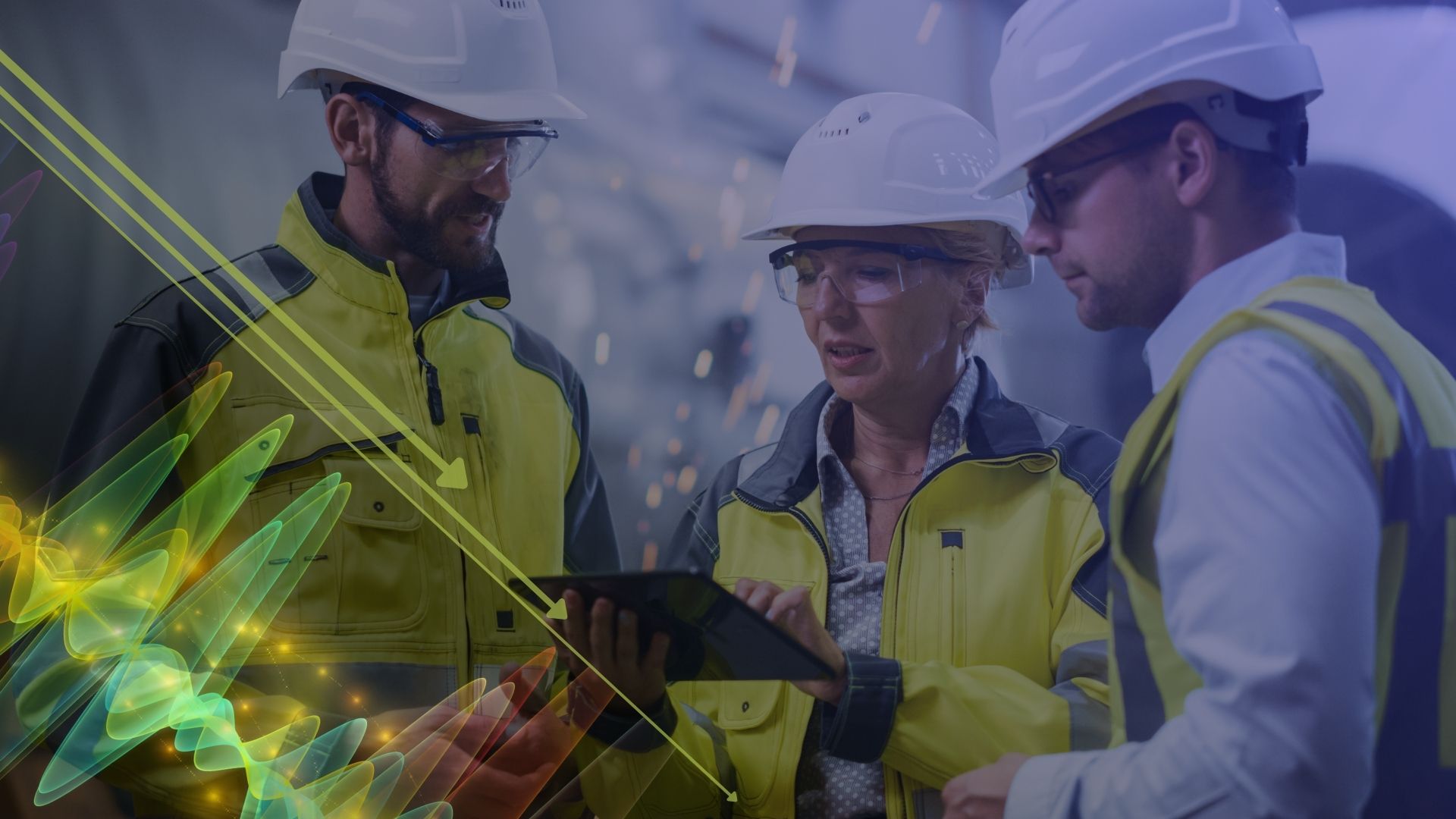
It is essential to monitor a machine's vibration levels over time to avoid serious issues
What is Seismic Monitoring?
Seismic monitoring is a useful technique for detecting machine vibration. Seismic monitoring involves using sensors that are placed on or near the machine to measure the vibrations that are produced. These sensors can be accelerometers, velocity sensors or other types of vibration sensors depending upon the application.
The data collected by the sensors can be analyzed to identify patterns and trends in the machine's vibrations. This can help to detect issues such as misalignment, unbalance, bearing wear, and other mechanical problems that can lead to increased vibration levels.
One approach to using seismic monitoring for machine vibration detection is to use machine learning algorithms to analyze the data from the sensors. These algorithms can be trained to recognize patterns and anomalies in the vibration data, and to provide early warning of potential problems before they become more serious.
Another approach is to use real-time monitoring and analysis to provide instant feedback to machine operators. This can allow them to adjust the machine's operation in real-time, to minimize the risk of damage or downtime. Overall, seismic monitoring can be an effective technique for detecting machine vibration and identifying potential issues before they become more serious. By combining these techniques with other methods, such as regular maintenance and inspection, it is possible to keep machines operating longer, and more efficiently to minimize the risk of unplanned downtime.
How Does Seismic Monitoring Equipment Work?
Seismic monitoring equipment can be used on machines to detect and monitor vibrations that are produced by the machine during normal operation. This equipment typically includes sensors that are mounted on the machine or near it, as well as data recording and analysis software.
The sensors used for machine vibration monitoring are chosen based on the application, typically velocity and acceleration transducers. These vibration transducers can be placed on various parts of the machine, such as the motor, bearings, and other components that are prone to vibration. The data collected by these transducers can then be analyzed to identify patterns and trends in the machine's vibrations. Vibration sensors produce a voltage output and vibration transmitters produce a 4-20 mA output.
One common approach to analyzing the data from seismic monitoring equipment on machines is to use vibration analysis software. This software can be used to process the raw sensor data and to identify specific vibration frequencies, amplitudes and phase angles that are associated with specific types of mechanical problems. For example, misalignment, unbalance, bearing wear, rotor to stator rubs, and other mechanical problems can all produce unique vibration signatures that can be identified through vibration analysis.
By monitoring the machine's vibration levels over time and comparing the data to established baseline levels, it is possible to detect changes in the machine's condition and identify potential issues before they become more serious. This can allow for early detection and intervention to prevent unplanned downtime, reduce the risk of damage to the machine and associated production losses.
Overall, seismic monitoring equipment is a valuable tool for machine maintenance and reliability, allowing for the early detection of mechanical problems and the optimization of machine performance.
Seismic Monitoring Systems
A seismic monitoring system also known as a vibration Condition Monitoring System (CMS) includes the vibration transducers, data acquisition systems, analysis software, and the alarm notification systems. These systems are outlined below:
• Transducers: Seismic transducers include sensors and transmitters. Vibration sensors that produce a voltage output, like velocity sensors and accelerometers, are typically used with monitoring systems, such as Vibration Monitoring Systems (VMS) or Machinery Protection Systems (MPS). Vibration Transmitters that produce a 4-20 mA output like velocity and acceleration transmitters are used with Control Systems, Programmable Logic Controllers (PLC), and/or Supervisory Control and Data Acquisition (SCADA) Systems.
• Data Acquisition (DAQ): The DAQ is responsible for collecting data from the sensors and converting it into a digital format that can be analyzed by software. The DAQ can include the VMS, the MPS, control systems, distributed control systems, PLCs, and SCADA systems.
• Analysis Software: The analysis software allows for the data collection by the vibration transducers to allow for identifying patterns and trends in the machine's vibratory behavior. This can include information such as the frequency, amplitude and phase of the vibration patterns, and can be used to identify potential mechanical problems such as misalignment, unbalance, bearing wear, rubs, or other issues.
• Alarm and Notification System: Once a problem is identified, the system can trigger an alarm or notification to alert the operator or maintenance personnel locally and remotely, allowing for early intervention to prevent unplanned downtime and reduce the risk of damage to the machine and production losses.
By continuously monitoring the machine's vibration levels over time and comparing the data to established baseline levels, seismic monitoring systems provide early warning of potential issues, allowing for proactive maintenance.
Overall, seismic monitoring systems are a valuable tool for machine maintenance and reliability, enabling the early detection of mechanical problems and the optimization of process performance.
Contact Metrix Vibration today if you have any questions about seismic vibration monitoring or want to learn more about machine condition monitoring equipment.