The Future of Seismic Sensors in the Vibration Monitoring Industry
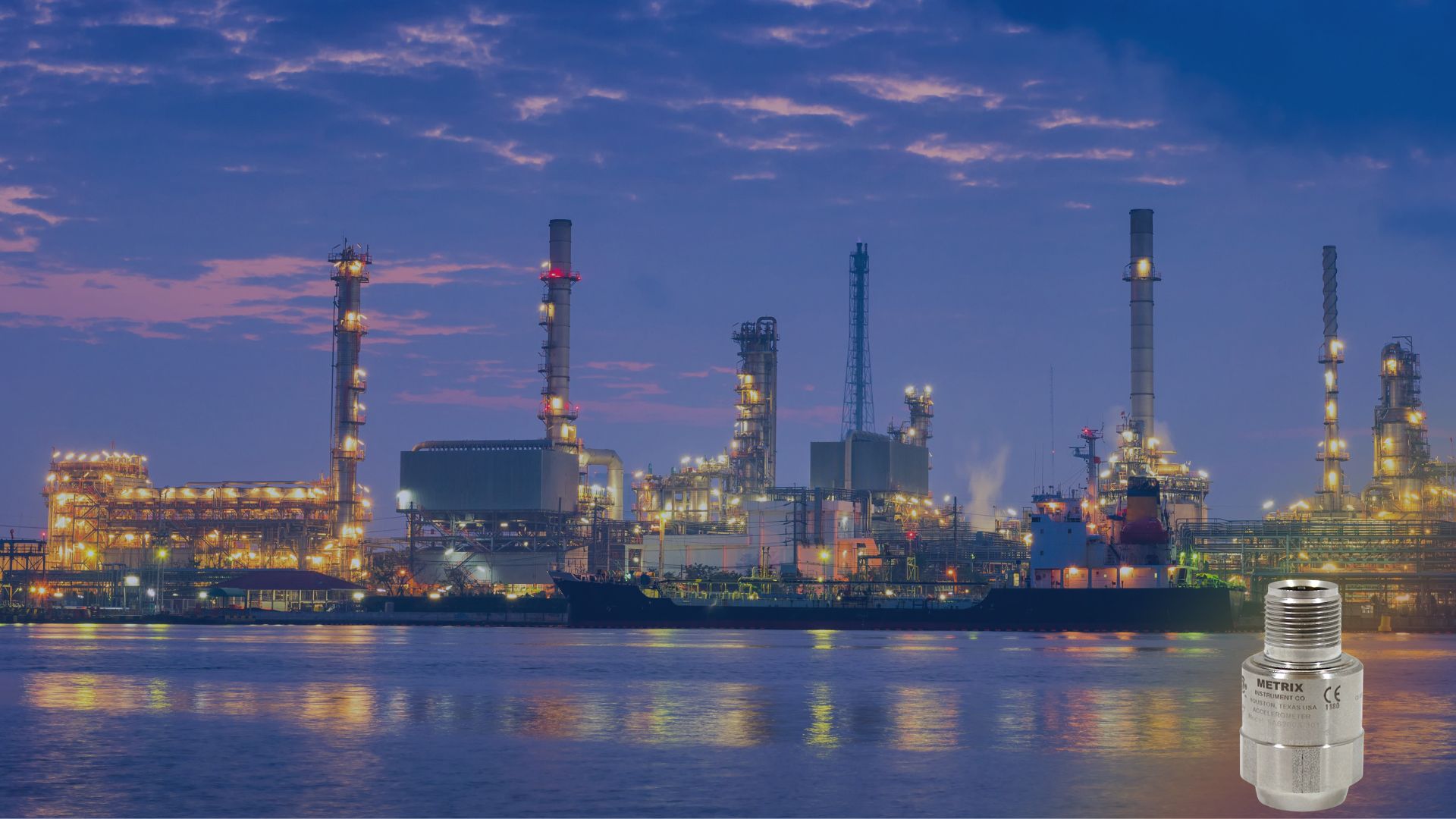
With technology evolving, Metrix seismic sensors hold a pivotal role when it comes to vibration monitoring
Vibration monitoring has proven its worth time and time again in industrial settings. These systems can be configured so employees can step in before vibration begins to destroy operations from the inside out.
As less people are being used in our industrial plants, and as automation takes a greater hold on industrial processes, there becomes a greater need to know the condition of your rotating and reciprocating machinery assets. The best way to monitor your machinery assets is with vibration monitoring.
Of all the components used to monitor equipment, seismic sensors have been taking center stage lately especially with rolling element bearing machines (we’ll talk about fluid film bearing machines and proximity sensors in another topic). Between the advancements in technology and their role in the cloud, sensors can revolutionize a variety of applications in several industries, including oil and gas, power generation, mining, construction, water and wastewater, as well as other industries. Let’s look at how the latest reports point to big changes in the near future.
6.3% CAGR from 2023 to 2028
The vibration monitoring market is forecasted to grow from $1.76 billion in 2024 to $2.39 billion in 2029. This growth is tied to the maintenance processes on various sites today. Better monitoring leads to improved predictive maintenance, reducing downtime, and increasing productivity.
Today’s seismic sensors boast improved accuracy and sensitivity using cloud-based analytics when compared to their counterparts of the past. Their trajectory is only likely to rise over the next half-decade. When production processes are harder to control and optimize than maintenance processes (at least, as of this writing), the logical conclusion would be for decision-makers to make investments that have proven themselves with compelling results.
Seismic Sensors Across Applications
Vibration monitoring sensors trigger alerts for both operational and mechanical failures or malfunctions. They measure vibrations either on an ongoing basis or at preset intervals. The vibration levels, at a minimum, include the amplitude of vibrations on rotating or reciprocating machines. In addition, frequency analysis can be used to track and interpret changes in machinery parts, including gears and bearings, to predict equipment failure.
From air compressors to steam turbines, vibration monitoring is playing a pivotal role in reimagining the work environments of today. Seismic sensor technology makes it possible to securely position these sensors so they can report real-time data back to a company. Instead of sounding false alarms several times a day, technicians, engineers, and operations managers quickly come to trust the system. Sensors are the key to cloud-based data analytics. It's a more precise way to measure what's happening inside the machinery, so technicians don't have to rely on sight and temperature checks alone.
Industries With Buying Power
While adopting more advanced technology, vibration monitoring varies by industry and company. There has been a strong trend for different verticals to allocate more budgetary funds to the equipment that protects their machinery. Better predictive maintenance makes for more reliable budget forecasting because the machinery runs better, allowing your process to run smoother and longer.
The oil and gas industry has been particularly ready to take advantage of the newest developments. Refineries and chemical plants can be hazardous to humans and animals, and there are numerous controls to ensure that the volatile gases and fluids stay where they’re designed to be, and that is the main reason vibration monitoring is employed in those industries. Plus, as the price of oil fluctuates, these companies are looking for ways they can keep costs low and productivity high.
While other industries will feel the rise in seismic sensors and vibration monitoring, it’s the oil and gas industry that’s likely to loom the largest in terms of sheer spending. Sensors and transmitters may be one part of vibration monitoring, but they're increasingly considered the bread and butter of predictive maintenance. The more agile they are, the more value they bring to the company and its customers.
Metrix Vibration Seismic Sensors: Reliable Now and Into the Future
At Metrix, our staff has seen how the technology has moved from one phase to the next, sometimes stalling, but ultimately moving forward. Our clients use our seismic equipment in a variety of facilities, and they each have their expectations during implementation. As the stakes increase, we stay on the cutting edge of development, ensuring our customers aren't left behind.
Accelerometers and Velocity Sensors from Metrix Vibration