Which Vibration Detection Device Should You Use? An Accelerometer or a Velocity Sensor?
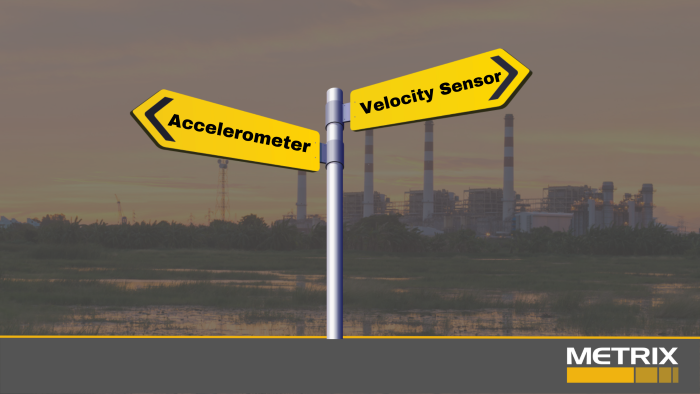
Learn how to choose the appropriate device to detect vibration as per your needs.
Harnessing the ability to measure vibration is critical in many industries. Being able to detect even the slightest changes in machine vibration can help avoid problems. Fortunately, we have many tools to help us do this, but, what good is having the technology if you don’t know how to use it?
As technology advances, we're faced with more and more choices when it comes to vibration monitoring equipment and different types of vibration sensors. It can be challenging to know if you need an accelerometer or a velocity sensor. By better understanding the different characteristics and functions of each, we'll be able to answer the question: When should you use an accelerometer versus a velocity sensor as your vibration detection device?
What is an Accelerometer?
An accelerometer is a device that measures the change in velocity over time of a reference mass. Using Newton’s Law, mass times acceleration equals force (F = m x a). Accelerometers can measure both the magnitude and direction of this force. They come in various shapes, sizes, sensitivity levels, and technologies. Some are small and lightweight, while others are large and robust. They can be used in a variety of applications, including automotive, aerospace, military, and industrial to measure vibration.
What is a Velocity Sensor?
A velocity sensor is a device used to measure the change in distance over time. As the vibration amplitude increases, the output of the sensor increases. Velocity sensors are also available in a variety of shapes, sizes, sensitivity levels, and technologies. They are commonly used for measuring the speed of moving objects, such as vehicles or machinery vibration.
In What Scenarios Would Someone Use an Accelerometer Over a Velocity Sensor?
The general rules of thumb are as follows:
- If you are interested in casing motion, you should use a seismic transducer (velocity sensor or accelerometer); your choice of which to use should be governed by considering the signal strength the transducer will provide at the frequency(ies) of interest.
- If the rotor can move relative to the casing, and you are interested in actual shaft motion, you must use a proximity probe.
Remember for a fluid film bearing machines you generally want to use shaft observing proximity probes, an exception is for reciprocating machines. Even though the reciprocating machines have fluid film bearings supporting the crankshaft, the machines are so stiff there is little to no relative motion between the crankshaft and the casing, so casing mounted transducers would be a better application in this case.
For rolling element bearing machines, there is very little relative motion between the rotor and the casing, so casing-mounted transducers are usually the best application. An exception is for slow-moving rotors that have very large rolling element bearings; in this case, a proximity probe may be the best sensor for machine conditions due to the slow shaft motion and the possibility of rolling-element bearing wear.
With the above fundamental understanding, the first thing you should consider is the machine type and the temperature environment the sensor will be mounted in. Accelerometers and certain velocity sensors are limited to 100 degrees Celsius (212 degrees Fahrenheit). Special accelerometers can go up to 325 deg C (617 deg F) and certain velocity sensors can go up to 375 deg C (707 deg F).
The next thing you have to consider are the frequencies of interest. For example, you want to capture the rotor related malfunctions that show themselves from 1/4X to 3X (X stands for the running speed of the machine), and if you are monitoring a rolling element bearing machine you would want to monitor 1 to 6 times the outer race ball pass frequency (BPFO). Typically, in 98% of the rolling element bearing machines in industry, if the machine operates at equal to or less than 60 Hz, use a velocity sensor, or if the machine operates at greater than 60 Hz use an accelerometer. An exception to this above guidance is with a speed increasing gearbox. The motor or prime mover might be operating at or less than 60 Hz, but the speed increasing gearbox creates frequencies that are higher than 60 Hz, so the use of an accelerometer is warranted.
For more details on transducer selection, please see the whitepaper “Accelerometers Versus Velocity Sensors – What's the Difference?” on our website.
Tips for Using an Accelerometer or Velocity Sensor for Vibration Detection
You might need to use either an accelerometer or a velocity sensor in various circumstances. Which one you decide to use will depend on the data you're trying to capture and monitor. Here are a few tips for using an accelerometer or velocity sensor:
- Establish what type of data you need to collect and review.
- Understand how each sensor works and what its benefits and limitations are.
- Always consult the manufacturer's guidelines for using accelerometers or velocity sensors.
- Be sure to check the calibration of vibration sensors before use.
- Test the sensor in various scenarios to ensure that it is performing correctly.
By understanding when to use an accelerometer or a velocity sensor, you can ensure that you're using the right tool for the job. Having the proper tools is essential for monitoring vibrations and preventing problems before they occur. Learn more about using accelerometers or velocity sensors to get the most out of your vibration monitoring system from Metrix Vibration.