How to Use Seismic Transmitters & Switches
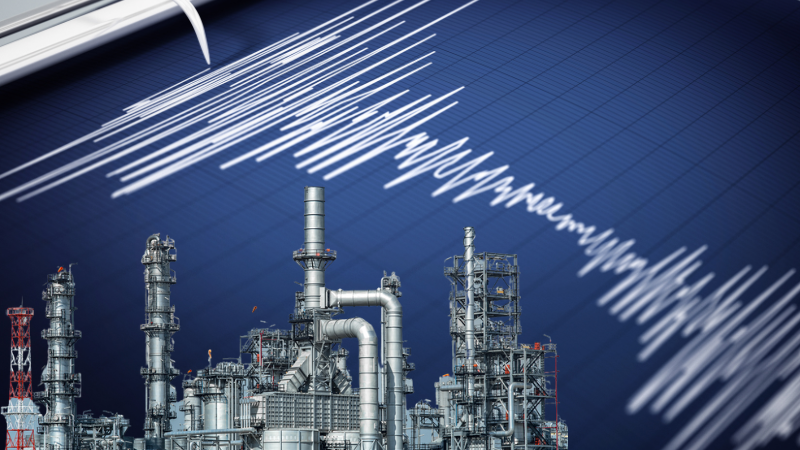
Wondering about seismic vibration monitoring and how to use it?
This blog post is focused on seismic transmitters and switches, usually used on rolling element bearing machines. These same seismic transmitters and switches can be used on reciprocating machines as well as in some cases on fluid film bearing machines.
Unscheduled downtime costs a business valuable time, productivity, and money. Depending on the reason for downtime, these losses can be short or long-term. Unscheduled downtime results in a loss of profitable output while your machinery is not functioning. This can add costs for standby labor, cause quality issues, necessitate emergency repairs, and may create safety concerns for employees. Worse, downtime can jeopardize customer trust and result in delivery delays.
Unscheduled downtime is, by nature, impossible to plan for. Unfortunately, it can also be an expensive inconvenience. However, although you can’t predict when downtime will occur, you can stay prepared by taking the necessary steps to prevent it.
Metrix Vibration has the monitoring systems needed to alert you to changes in machine condition well in advance of impending or imminent failure. Using seismic monitoring equipment can help reduce the duration of unscheduled downtime which results in quality operations, expediting repairs, remediating safety concerns, and improving delivery.
The Metrix Vibration Methodology
Metrix vibration methodology makes vibration monitoring easy by employing the right number of sensors for the application for early warning of an impending machine problem. We create solutions that make economic sense, prioritizing prevention and proactivity over reactivity.
For machinery that has a critical role in your production, Metrix Vibration advocates for a high-value solution. These solutions will monitor each movement of your machine from every rotation, thrust and throw. Our high-value seismic sensors mirror the high-value equipment used in your plant — the more critical the machine, the more intensive the monitoring solution we advocate. This can save you money and provide value both in the short and long-term.
We advocate using lesser number of sensors for non-critical machinery that only marginally impacts plant productivity. This solution still monitors and protects your equipment, but at a level that mirrors the machine’s return on your investment. As you can see, at Metrix Vibration, we believe in selling value, not just products.
How Seismic Transmitters & Switches Help Minimize Unscheduled Downtime
Seismic transmitters and switches can help you minimize unscheduled downtime. Here’s how these components can prevent critical downtime issues.
Seismic Transmitters
Seismic transmitters provide a 4-20 mA output to your control system (e.g. PLCs, SCADA systems, RTUs etc.). This 4-20 mA output can be trended along with the other machine parameters like speed, pressure, temperature, flow, power level and other process parameters. This gives an operator a better understanding of what is going on with the machine. Under steady state conditions of speed and power level, the vibration levels should not be changing significantly. From a statistical perspective under steady state conditions, the vibration level should not change more than two standard deviations from the average (mean) vibration value. If the vibration value changes by more than two standard deviations from the mean, an investigation into why the vibration is changing is warranted.
Under non-steady state conditions, the 4-20 mA output needs to be balanced with the other process variables to determine if an abnormal vibration situation is present. Vibration levels can change when the machine is subject to changes in speed, load and other major process variable changes.
Seismic Switches
Seismic switches can be mechanical or electrical in nature and are used to protect rotating and reciprocating machinery. A mechanical switch is used to prevent catastrophic failure and provide personal safety. A mechanical switch does not provide early warning of an impending failure. They are considered a catastrophic failure device. In other words, when a mechanical switch activates to protect a machine, it is usually after mechanical damage has occurred to the machine. Whereas in an electronic switch, the protective device can be setup to monitor vibration specific to the machine in terms of inches per second or millimeters per second based on known vibration values. An electronic switch can be setup to be much more sensitive than a mechanical switch.
Electronic switches offer a predictive maintenance strategy whereas a mechanical switch fits into a more preventive maintenance strategy. Preventive maintenance is where machines are repaired periodically, but not necessarily based on their condition. Although a preventive maintenance strategy is less expensive than a run to failure strategy, in some cases, preventive repairs can cause more damage than just leaving a machine alone. The best maintenance strategy is predictive in nature and the electronic switch is more conducive to that strategy. Keep in mind, the mechanical and electronic switches do not collect vibration data but are usually paired with a manual vibration data collection process.
We have found that combining the electronic switch with a 4-20 output is a powerful combination to protect or manage a machine.
Electronic Switches with 4-20mA Output
In a proactive maintenance strategy, an electronic switch combined with a 4-20 mA output to your control system (e.g. PLC, SCADA system, RTU etc.), provides the actionable information you need to take positive action.
This monitoring solution is usually permanently mounted on the load side of the machine, it could be the switch itself or a sensor, like an accelerometer, connected to an electronic switch. The electronic switch that includes a 4-20 mA output, is like a transmitter that is integrated with the plant information network that offers a predictive maintenance and possibly a proactive maintenance strategy. When the vibration 4-20 mA output is combined with the plant information network, a proactive maintenance strategy can be realized. This 4-20 mA electronic switch option provides the most cost-effective maintenance strategy above the other mechanical and electronic switches. It is great for rotating and reciprocating machinery. The electronic switch combined with the 4-20 mA output provides actionable information via early warning of a vibration issue, plus diagnostic information accessible by portable tools.
Contact Metrix Vibration Today
This blog post focused on seismic transmitters and switches, usually used on rolling element bearing machines. These same seismic transmitters and switches can be used on reciprocating machines as well as in some cases on fluid film bearing machines.
Unscheduled downtime can cost you more than productivity. Be prepared and minimize your unscheduled downtime by using seismic transmitters and switches. Contact Metrix Vibration to identify the right seismic monitoring equipment for your needs today.